Work Processes and Practices: Difference between revisions
Rebekah Hook (talk | contribs) |
Rebekah Hook (talk | contribs) |
||
Line 90: | Line 90: | ||
==== [[APPENDIX 1: Use of Mobile Phones|APPENDIX 1: Personal Safety Guidance for Staff Working Alone]] ==== | ==== [[APPENDIX 1: Use of Mobile Phones|APPENDIX 1: Personal Safety Guidance for Staff Working Alone]] ==== | ||
== | == Manual Handling == | ||
==== Policy ==== | ==== Policy ==== | ||
Line 131: | Line 131: | ||
The aim of this guidance is to provide employers and manual handling co-ordinators with guidance on how to take the necessary steps to comply with the regulations. | The aim of this guidance is to provide employers and manual handling co-ordinators with guidance on how to take the necessary steps to comply with the regulations. | ||
==== Identification of manual handling activities ==== | ===== Identification of manual handling activities ===== | ||
The first stage is to identify any manual handling activities which occur within the workplace or are undertaken by your employees at work. You should also include any manual handling activities which occur away from your normal place of work. | The first stage is to identify any manual handling activities which occur within the workplace or are undertaken by your employees at work. You should also include any manual handling activities which occur away from your normal place of work. | ||
Line 151: | Line 151: | ||
If the manual handling activity involves twisting, i.e. moving the upper part of the body while keeping the feet static, and the frequency of lifting does not exceed 1 lift every two minutes and there are no posture constraints, then the guideline weights should be reduced by 10% when twisting through 45 degrees and 20% when twisting through 90 degrees. | If the manual handling activity involves twisting, i.e. moving the upper part of the body while keeping the feet static, and the frequency of lifting does not exceed 1 lift every two minutes and there are no posture constraints, then the guideline weights should be reduced by 10% when twisting through 45 degrees and 20% when twisting through 90 degrees. | ||
If the manual handling activity involves twisting and stooping/bending then the guideline weights should be reduced by 50%. If the guideline weights are exceeded then a more detailed risk assessment should be made as this is particularly stressful on the back. | If the manual handling activity involves twisting and stooping/bending then the guideline weights should be reduced by 50%. If the guideline weights are exceeded then a more detailed risk assessment should be made as this is particularly stressful on the back. |
Revision as of 14:16, 9 January 2025
Lone Working
Policy
We recognise the importance of ensuring that all lone working activities are managed appropriately to minimise risk. The safety of workers will always be carefully considered in lone working situations and we will ensure they are capable of responding correctly to emergencies. Such emergencies may arise due to fire, equipment failure, illness, accidents and unauthorised intruders. We will assess the potential hazards from lone working and take appropriate action to ensure adequate control measures are in place to reduce risk. We will take into account not only the task but also the abilities and experiences of those who may be undertaking the work. The findings of the risk assessments will determine the level of supervision required. To ensure that lone workers are not at more risk than other employees we will provide adequate training on understanding the risks and avoiding panic reactions to unusual situations. Checks will be made to ensure that any lone workers have no medical condition which makes them unsuitable for lone working. We will not permit lone working where risks cannot be controlled to an acceptable level. Procedures will be put in place to monitor lone workers to see they remain safe. We will regularly review and, where necessary, modify our assessments, especially where we have reason to suspect that they are no longer valid or there has been a significant change in the work to which the assessment relates.
Arrangements for Lone Working
The Lone Working Co-ordinator will ensure that:
1.1 All employees likely to work alone are identified.
1.2 Consultation with employees regarding lone working takes place.
1.3 The tasks which expose employees to lone working are identified and listed.
1.4 The hazards to which employees may be exposed are suitably and sufficiently assessed.
1.5 Adequate control measures are implemented to prevent ill health and accidents.
1.6 A decision based on the risk assessment findings is made to determine the level of supervision required.
1.7 Activities requiring special arrangements in order to monitor the safety of lone workers are identified.
1.8 Activities which must not be performed by lone workers are identified and brought to the attention of all relevant persons.
1.9 Employees that work alone are given adequate information, instruction and training.
1.10 Checks are made to ensure that any lone workers are medically fit for the tasks.
1.11 Control measures are regularly monitored maintained to ensure they remain effective.
Guidance and Records
Lone Working Activities
Lone working represents a situation where a person has neither visual nor audible communication with someone else who can offer immediate assistance in the event of an accident, illness or other emergency. The guidance contained in this section of the policy relates to lone working situations conducted in the normal workplace of the organisation. It may be necessary to consult the “Home/Remote Workers” if you employ staff who work from home or remotely away from the normal workplace.
Lone workers must receive appropriate training and have the necessary experience before being allowed to work alone.
All lone workers should be aware of the following as part of their safety induction training:
- Emergency contact numbers
- Accident/incident reporting procedure
- Restrictions on lone working
- Specific precautions and arrangements considered necessary for some lone working activities.
Low Risk Activities
Lone working activities should be restricted, where possible, to activities presenting a low risk; even in the event of control measures failing, e.g. persons working alone in offices outside normal working hours are unlikely to be at significant risk provided that appropriate fire and security precautions are in place. Indeed, there is no evidence that this type of lone working activity presents an unacceptable risk requiring special monitoring arrangements, any more than many other activities that individuals undertake alone outside work. It is good practice for those individuals working outside normal working hours to inform a friend or family member of their location and approximate time of return.
It is also acceptable for low risk activities to be performed by a lone worker provided the person performing the task is:
- Competent (i.e. has the necessary experience and has received appropriate training)
- Capable of dealing with any reasonably foreseeable accident or other emergency alone, without the assistance of colleagues.
Higher Risk Activities
There are occasions when it is not appropriate for activities to be performed by lone workers unless special arrangements involving help or back up are introduced.
Special arrangements must be considered for all activities where it is judged that the risk cannot be adequately controlled by one person. A formal risk assessment is required for these higher risk lone working activities, including a description of arrangements needed to ensure the work can be carried out safely.
Prohibited Lone Working Activities
Lone working must not be undertaken where there is a high risk that the work might result in an accident which would be sufficiently serious to require a second person to be available to summon help.
Those tasks that are considered unacceptable for a lone worker to perform under any circumstances must be documented in the lone working risk assessment.
Individuals at Special Risk
Lone working activities are often inappropriate for certain individuals or groups of workers, e.g. individuals with a known medical condition, those with limited experience or training.
Special Arrangements to Consider for Higher Risk Lone Working Activities
Special arrangements are required for higher risk lone working activities. These should be considered for all activities where it is judged that the risk cannot be controlled adequately by one person.
Although lone workers cannot be subject to constant supervision, it is important that proportionate measures are selected to monitor the safety of individuals engaged in these higher risk activities.
These include:
- Periodic monitoring of lone workers by the supervisor or other colleague
- Lone workers logging in and out with their manager and providing an indication of the likely duration of the work
- Regular contact between the manager and lone worker via telephone
Summary of Requirements
Provided that the lone working activity presents a low risk, and the line manager considers the individual competent to be working alone, the activity can go ahead without the need for any special arrangements.
If the lone working activity presents a high risk, it needs a formal assessment to identify the appropriate arrangements that are needed to ensure the safety of the lone worker.
High-risk activities are those where there is a reasonably foreseeable risk that the work might result in an accident which could be sufficiently serious to require a second person to be available to summon help. These must not be undertaken by a lone worker. These activities must be brought to the attention of workers as part of their local induction training.
Examples of high-risk activities that must not be undertaken by the lone worker include:
- use of machinery that could result in serious injury in the event of an accident
- use of hazardous substances that present a risk of serious acute health effects in the event of exposure
APPENDIX 1: Personal Safety Guidance for Staff Working Alone
Manual Handling
Policy
We will, so far as is reasonably practicable, avoid the need for any employee to undertake any manual handling operations which involve a risk of their being injured. Where this is not reasonably practicable, we will carry out a suitable and sufficient assessment of all such operations and take appropriate steps to reduce the risk of injury to the lowest level that is reasonably practicable. We will provide information to our employees on the weight and centre of gravity of the loads they are required to handle and will ensure that all employees who carry out manual handling operations are provided with information on the findings of the assessments and are trained in safe lifting and handling techniques and the use of lifting equipment. We will ensure that all employees make full and proper use of any systems of work provided. We will review the assessments regularly and, in particular, when there is a significant change in the operations to which they relate or if there is any reason to suspect that they are no longer valid.
Arrangements for Manual Handling
The Manual Handling Co-ordinator will ensure that:
1.1 Where manual handling activities cannot be avoided by elimination, mechanisation or automation, initial manual handling assessments are conducted to identify those areas which require further in-depth assessment.
1.2 In-depth assessments are undertaken for those tasks that pose a significant risk such that they may be eliminated or mechanised.
1.3 Risks are reduced by using safe systems of work for those tasks which cannot be completed without manual handling.
1.4 An action plan is drawn up and a budget set, where necessary, for any new measures that are required.
1.5 Information, practical instruction and training on safe lifting techniques is provided for all persons identified in the assessment process as potentially being at risk.
1.6 Assessments are recorded, maintained and reviewed on a regular basis to ensure compliance with current legislation and best practice.
1.7 Loads delivered to the company are correctly packaged, labelled with the weight, secured in strong containers and provided in such condition as to enable the safe removal, placement, loading, unloading and handling of the load.
1.8 Employees are fit to undertake the work they do.
1.9 Adequate information, instruction and training is provided for the use of any equipment that may be necessary to conduct particular tasks.
1.10 External competent persons are consulted, where necessary, to assist with assessments, developing codes of practice and health surveillance.
1.11 Procedures are in place for ensuring the health and safety of those persons at increased risk from manual handling operations, e.g. new and expectant mothers and those with particular medical conditions.
Guidance and Records
Introduction
The main aim of the Manual Handling Operations Regulations is to prevent injury, not only to the back, but to any part of the body. The Regulations apply to the manual handling of loads which require human effort, which include transporting a load, supporting a load in a static posture, lifting, lowering, dropping, pushing and pulling a load.
Manual handling activities are common throughout the workplace and account for more than a third of all over three day reportable injuries. Manual handling injuries not only affect the back, neck and shoulders, but the lower limbs, often as a result of the load being dropped. Often manual handling injuries occur over a period of time due to poor manual handling techniques and not as a result of a single event.
Under the Manual Handling Operations Regulations, all manual handling activities which involve a risk of injury should be avoided where possible. If it is not possible to avoid the activity by elimination, automation or mechanisation, then an assessment of the risk should be carried out and the risks reduced to the lowest level possible.
The aim of this guidance is to provide employers and manual handling co-ordinators with guidance on how to take the necessary steps to comply with the regulations.
Identification of manual handling activities
The first stage is to identify any manual handling activities which occur within the workplace or are undertaken by your employees at work. You should also include any manual handling activities which occur away from your normal place of work.
Once the manual handling activities have been identified, it is then necessary to decide if each activity poses a significant risk of injury to the employee and whether a further, more detailed manual handling assessment is required.
If it is not possible to avoid the manual handling activity by elimination, automation or mechanisation then it may be necessary to carry out a more detailed assessment.
In order to decide if the manual handling activity poses a significant risk of injury to the employee you may wish to consult the risk assessment diagram below. It should be noted that the weights in the risk assessment filter are only guidelines and apply to the lifting and lowering of loads.
Risk Assessment Diagram
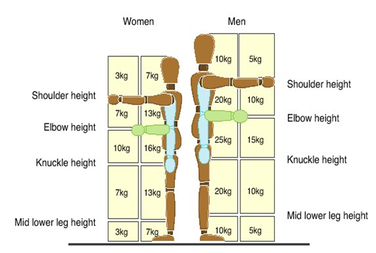
The guideline weights given in the diagram to the right are based on providing reasonable protection for 95% of working men and women. If the manual handling activity involves moving the load between different body reference points then you will need to take the lowest weight.
The guideline weights in the risk assessment diagram above apply for the lifting and lowering of loads and assume that the load is easy to grasp with both hands, the operation takes place in reasonable working conditions and the handler is in a stable body position and the frequency of lifting does not exceed one lift every two minutes.
If the frequency of the manual handling activity is increased then it will be necessary to reduce the guideline weights by 30% for two lifts per minute, 50% for eight lifts per minute and 80% for 12 lifts per minute.
Even if the above conditions are satisfied, a more detailed risk assessment should be made where the employees have no control over the pace of work, pauses for rest are inadequate or the handler has to support the load for any length of time.
If the manual handling activity involves twisting, i.e. moving the upper part of the body while keeping the feet static, and the frequency of lifting does not exceed 1 lift every two minutes and there are no posture constraints, then the guideline weights should be reduced by 10% when twisting through 45 degrees and 20% when twisting through 90 degrees.
If the manual handling activity involves twisting and stooping/bending then the guideline weights should be reduced by 50%. If the guideline weights are exceeded then a more detailed risk assessment should be made as this is particularly stressful on the back.
Guidelines for carrying
The guideline weights in the risk assessment diagram above apply to carrying operations where the load is held close to the body and is carried no further then 10 metres. Where the load can be carried securely on the shoulder without first having to be lifted, then the guideline weights can be applied to carrying distances in excess of 10 metres.
A more detailed risk assessment should be made for all carrying operations if the load is carried over a longer distance without resting or the hands are below knuckle height or above elbow height.
If at any time during the manual handling activity the guideline weights are exceeded, then a more detailed manual handling assessment will need to be carried out. It should be noted the key duty of the employer is to avoid hazardous manual handling activities and where these cannot be avoided then a more detailed manual handling assessment will need to be undertaken with the aim to reduce the risk to employees.
Employees’ Responsibilities
The co-operation and assistance of all employees is of the utmost importance. The recommendations of the employees undertaking the tasks will form an important part of the assessment and where practicable will be implemented during any alteration to the work environment, practices or equipment.
It is the employees’ duty to:
- Take reasonable care for their own safety and that of colleagues when handling loads
- Follow the written assessments
- Never lift a weight that is beyond their capability
- Only use lifting and handling techniques in which they have been trained
- Use lifting and handling aids in accordance with training and instructions
- Always visually inspect equipment for damage and defects prior to use and report any defects immediately
- Never undertake any task they do not feel confident in
- Check with managers if they are unsure about any aspect of manual handling
- Alert managers to any situation which might present a serious or imminent danger.
Health Problems
Where any person suffers ill-health or is involved in an accident, they must report it to management immediately. This is to allow the duties to be re-assessed and adapted as far as reasonably practicable. All such information will be kept in the strictest of confidence.
Management will ensure that ill-health, manual handling accidents/incidents are investigated and subsequent action implemented to prevent recurrence and all persons concerned informed of those actions.
Where appropriate, health surveillance will be used to monitor certain individuals who have been identified as being particularly at risk and where ill-health effects have been identified.
Pregnancy
Female staff must notify management of pregnancy to ensure their tasks will not cause any detrimental health effect to themselves or their unborn child.
All such information will be in the strictest confidence and, as a result, changes of work or routine may have to be introduced to reduce any risk identified.
Good Handling Techniques
Think before lifting/handling. Plan the lift. Can handling aids be used? Where is the load going to be placed? Will help be needed with the load? Remove obstructions such as discarded wrapping materials. For a long lift, consider resting the load midway on a table or bench to change the grip.
Keep the load close to the waist. Keep the load close to the body for as long as possible while lifting. Keep the heaviest side of the load next to the body.
Adopt a stable position. The feet should be apart with one leg slightly forward to maintain balance. The worker should be prepared to move their feet during the lift to maintain stability. Avoid tight clothing or unsuitable footwear, which may make the lift difficult.
Get a good hold. Where possible the load should be hugged close to the body. This may be better than gripping it tightly with hands.
Start in a good posture. At the start of the lift, slight bending of the back, hips and knees is preferable to fully flexing the back (stooping) or fully flexing the hips and knees (squatting).
Avoid twisting the back or leaning sideways, especially whilst the back is bent. Shoulders should be kept level and facing in the same direction as the hips. Turning by moving the feet is better then twisting and lifting at the same time.
Keep the head up when handling. Look ahead, not down at the load, once it has been held securely.
Move smoothly. The load should not be jerked or snatched as this can make it harder to keep control and can increase the risk of injury.
Don’t lift or handle more than can be easily managed. There is a difference between what people can lift and what they can safely lift. If in doubt seek advice or get help.
Put down, and then adjust. If precise positioning of the load is necessary, put it down first and then slide it into the desired position.
Personal Protective Equipment (PPE)
Policy
We will identify and assess all activities our employees may be required to undertake during the course of their employment with us. Following the amendments to The Personal Protective Equipment at Work Regulations 2022 we will now extend this to cover casual or irregular workers (such as Labour Only). We will only specify personal protective equipment as the last means of defence should we be unable to otherwise eliminate the risk to our employees. We will, as far as is reasonably practicable, implement the hierarchy of control measures. Personal protective equipment will only be provided if the risk to our employees cannot be adequately controlled after the hierarchy of control measures has been exhausted. If and when we do provide personal protective equipment, we will ensure it is fit for the purpose and environment it is to be used in and that it fits the wearer correctly to give the level of protection the equipment was so designed for. We will ensure employees are consulted on the type of personal protective equipment to be used and that they are given adequate and sufficient information, instruction and guidance on the use, storage and maintenance of such equipment. We acknowledge our duty to provide personal protective equipment to all employees, including casual or irregular workers, as may be necessary and that such equipment will be free of charge. Where it is identified that an employee’s well-being may be affected due to exposure to a specific hazard or hazards, a medical questionnaire will be completed. We will ensure where necessary that regular health surveillance is provided where the risk of harm to our employees is controlled by the use of personal protective equipment.
Arrangements for Personal Protective Equipment
The Personal Protective Equipment Co-ordinator will ensure that:
1.1 All activities our employees (including casual or irregular workers) may be required to undertake during the course of their employment are identified and assessed to determine the need for Personal Protective Equipment (PPE).
1.2 As far as is reasonably practicable, the hierarchy of control measures i.e. elimination, reduction, substitution, isolation or engineering controls, is followed to control the hazards that have been identified.
1.3 PPE is specified as a last form of defence only when the hierarchy of controls has been exhausted.
1.4 Where PPE is provided, it is fit for the purpose and the environment it is to be used in and it fits the wearer correctly.
1.5 Individuals or groups of people whose well-being may be affected due to exposure to a specific hazard or hazards are identified and a medical questionnaire is completed prior to any person commencing work in such an environment which may present a risk to them.
1.6 Where identified by the medical questionnaire, or where necessary due to the identification that the risk of harm is controlled by the use of PPE, health surveillance is provided at regular intervals.
1.7 Where PPE is required, it is provided free of charge.
1.8 Employees (including casual or irregular workers) are consulted on the type of PPE to be used.
1.9 All employees (including casual or irregular workers) required to wear PPE are given adequate and sufficient information, instruction and guidance on the use and maintenance of such equipment.
1.10 A procedure is in place to allow PPE provided to be maintained in good working order and/or adequate stocks of equipment are available to replace as necessary any damaged or worn equipment.
1.11 Suitable and sufficient facilities are provided to enable employees to store any PPE provided to them whilst not in use.
1.12 Where necessary, suitable and sufficient facilities are provided to permit employees to change from (and store) their normal clothing to specified personal protective clothing.
*Medical questionnaires cannot be issued pre-employment but can be issued post engagement.
Guidance and Records
Personal Protective Equipment (PPE)
Personal protective equipment (PPE) is defined in the regulations as ‘all equipment (including clothing affording protection against the weather) which is intended to be worn or held by a person at work and which protects him/her against one or more risks to their health or safety’. This includes high visibility clothing, eye protection, head protection, safety footwear, safety harnesses, hand protection, etc.
PPE should only be issued to the person who is going to use it, it cannot be shared. A register of issue and subsequent inspection should be maintained and means for the employee to keep equipment in a clean and hygienic condition should be provided.
Employees (including casual or irregular workers) cannot be charged by their employer for items of PPE they require to safely carry out their work activities.
Suitability of PPE
The right type of PPE should be selected, which can be done giving consideration to the following:
- Is it appropriate for the risks and conditions where employees are exposed to the risk?
- Does it prevent or adequately control the risks?
- Where more than one form of PPE is worn, are they compatible?
- What are needs of the job, and the demands it places on the wearer?
- Does it fit the wearer correctly?
- Has the state of the wearer’s health been considered?
Advice on the different types of PPE available and their suitability can be obtained from PPE manufacturers and suppliers, or your Health and Safety Consultant.
Training
Employees (including casual or irregular workers) who are required to wear PPE must be given adequate and sufficient information, instruction and guidance which should include the following areas:
- Training and instruction on how to use it properly.
- Why the PPE is needed – what the risks are, when PPE is to be used, repaired or replaced and its limitations.
- The importance of wearing PPE when exposed to the risk, without exception.
- Checking PPE is being used and taking action when it is not.
- Clear rules on what action will be taken if employees are not wearing the necessary PPE.
- Display of safety signs, reminding employees to wear PPE.
Respiratory Protection
Where respiratory protective equipment incorporating a tight fitting face-piece is provided to prevent exposure to hazardous substances, it must fit the wearer properly to provide full and adequate protection and therefore a face fit test must be conducted. A tight fitting face-piece is a full-face mask, a half-face mask, or a filtering face-piece (e.g. disposable mask), irrespective of whether they are used in negative pressure respirators, power assisted respirators or compressed air supplied breathing apparatus.
The face fit test will assess the fit by determining the degree of face-seal leakage of a test agent whilst the user is wearing the face-piece and undergoing certain physical exercises. Dependent on the respirator type in use, the test can be quantitative or qualitative, both of which require specialist equipment and trained operatives. Once face fit tested to a particular respirator (type and manufacturer) a certificate of test must be obtained and this recorded. Operatives do not require to be re-tested unless their facial characteristics change significantly (e.g. weight loss, major dentistry), the certification of test may pass from employer to employer, but the operative must only wear that type and manufacture of respirator that he/she was tested on. If an employee wears more than one type of tight fitting face-piece then each type of face-piece should be subjected to fit testing.
Fit testing is not required where a risk assessment clearly demonstrates that respiratory protective equipment is being worn for ‘comfort’ rather than as a control measure.
Loose fitting face-pieces, whose performance relies on sufficient airflow through the face-piece, do not require fit testing. However, the loose fitting face-piece must be of the correct size for the wearer to ensure adequate protection. Loose fitting face-pieces are better suited to those wearing spectacles with side arms and people with facial hair in the region of the face seal of a tight fitting mask. In the vast majority of scenarios loose fitting alternatives to tight fitting masks are available and should be selected where necessary.
Head Protection
Head protection should be worn whenever there is a risk of injury to the head from falling objects or hitting the head against something.
Where an assessment identifies the need for head protection it should meet the following criteria:
- Suitable for its intended purpose
- Appropriate size
- Have chin straps etc. where necessary
- Provide adequate levels of comfort
Head protection should be replaced at intervals recommended by the manufacturer or if it has received a severe impact, has been badly scratched or has cracked.
A follower of the Sikh religion is exempt from any legal requirement to wear a safety helmet while on a construction site ("any place where building operations or works of engineering construction are being undertaken"), provided that he is wearing a turban.
Eye Protection
There are different types of eye protection to cover different hazards. The following are examples of protection that may be required in certain circumstances:
- Safety spectacles incorporating sideshields
- Eyeshields
- Safety goggles
- Face shields
The following activities are likely to require the provision of eye protection:
- Handling acids, alkalis, corrosive substances etc.
- Using abrasive wheels, hand grinders etc.
- Welding operations
- Using gases or vapour under pressure
- Using laser equipment
Foot Protection
Safety footwear can come in the form of boots or shoes and purpose designed Wellington boots and there are different types to protect from different hazards. The following list gives examples of areas where safety footwear may be required:
- Workplaces where heavy objects have to be physically handled
- Areas where hazardous and/or corrosive chemicals are handled
- Workplaces where walking surfaces are unavoidably slippery
Ensure that the footwear chosen has the correct features to adequately protect against the identified hazards. Features can include:
- Protective toe-caps
- Penetration-resistant mid-soles
- Non-slip soles
- Heat-resistant soles
Consideration must also be given to other aspects including the material (e.g. leather or trainer-style), ankle support, and whether lace-up or slip-on is acceptable.
Hand and Arm Protection
Hand and/or arm protection may be required in the following circumstances:
- Manual handling of objects, machinery or equipment with abrasive or sharp areas
- Operating vibrating machinery such as orbital sanders
- Outdoor work
- Handling hot or cold materials
- Handling chemicals
- Where there is a risk of skin infection, disease or contamination
Hand and/or arm protection should be chosen to ensure it is appropriate to both the wearer and the hazard. Be sure not to introduce additional hazards through its use, such as through gloves that protect against cuts but may become entangled in machinery or prevent adequate dexterity.
Be aware that latex, in particular powdered latex, gloves are a known cause of sensitisation. The Health and Safety Executive (HSE) says that: "Single use, disposable natural rubber latex gloves may be used where a risk assessment has identified them as necessary. When they are used they must be low-protein and powder-free." Latex gloves may be considered necessary to protect against the transmission of blood borne pathogens.
If you are not in an industry where you come into contact with blood borne pathogens you should consider using alternatives to latex gloves, such as nitrile or vinyl gloves.
Protective Clothing
The following non-exhaustive list gives examples of circumstances where specific protective clothing may be required:
- Handling chemicals
- Working in the dark or low-light levels
- Working in food preparation areas
- Working near or in water
- Working in dusty environments
Protective clothing is likely to be needed to protect against hazards such as temperature extremes, adverse weather, chemical or metal splashes, spray from pressure leaks or spray guns, impact or penetration, contaminated dust, excessive wear or entanglement of own clothing. Such clothing can take the form of conventional or disposable overalls, boiler suits, specialist protective clothing, e.g. chain-mail aprons, high-visibility clothing, or may be needed to protect a specific body area such as leggings, gaiters, or spats for the legs.
Pressure System
Policy
We recognise that Pressure Systems have the potential to cause significant injury or damage to property in the event of system or component failure resulting in unexpected release of stored energy. We further recognise that it is extremely important that the system is correctly installed and used, maintained, and subject to thorough examination and test.
We will ensure that pressure systems are installed by a competent person and in positions that would minimise injury and damage in the event of unexpected releases of stored energy, and that the safe operating limits of pressure systems are established prior to first use and are clearly marked on the system. All operators will be given adequate and suitable instruction on the safe operation of pressure systems and any emergency procedures.
We will ensure that a competent person prepares a written scheme of examination for systems above 0.5 bar, including pipe work, where steam or fluid is stored. This will also be done for a compressed air receiver, and the associated pipework, where the product of the pressure in bars multiplied by the internal capacity in litres of the receiver is equal to or greater than 250 bar litres, and other applicable systems.
A competent person will carry out all maintenance, thorough examinations and tests as prescribed in the written scheme of examination.
Any necessary repairs arising from any reports on the condition of the systems or from any fault reporting system will be completed without delay. Any systems that are not subject to a written scheme of examination will be maintained in accordance with the manufacturer’s recommendations. We will ensure that all relevant records e.g., manufacturers safety information, written schemes of examination, examination reports etc, are retained for inspection.
Arrangements for the Safe Use of Pressure Systems
The Pressure Systems co-ordinator will ensure that:
1.1 Pressure systems are installed by a competent person and in positions that would minimise injury and damage in the event of unexpected releases of stored energy.
1.2 The safe operating limits of pressure systems are established prior to first use and that they are clearly marked on the system.
1.3 All operators are given adequate and suitable instruction on the safe operation of pressure systems and any emergency procedures.
1.4 A competent person prepares a written scheme of examination for systems above 0.5 bar, including pipe work, where steam or relevant fluid is stored.
1.5 A competent person carries out all maintenance, thorough examinations and tests as prescribed in the written scheme of examination.
1.6 Any necessary repairs arising from any reports on the condition of the systems or from any fault reporting system are completed without delay.
1.7 Any systems that are not subject to a written scheme of examination are maintained in accordance with the manufacturer’s recommendations.
1.8 All relevant records e.g., manufacturers safety information, written schemes of examination, examination reports etc, are retained for inspection.
Guidance and Records
Users and owners of pressure systems are required to demonstrate that they know the operating procedures of their pressure systems and that the systems are safe at their premises.
The Pressure Systems Safety Regulations use the terms "owner" and "user" with respect to the written scheme of examination. The primary duty is placed on the "user" in the case of fixed systems and the "owner" in the case of mobile systems. Both users and owners can be employers or self-employed persons.
Any pressure system covered by the regulations must have a written scheme of examination prepared by a competent person who has the appropriate technical expertise and knowledge. Serious accidents have occurred when systems have been over pressurised or exploded due to undetected internal corrosion and also leaks of steam and hot water have resulted in severe scalds.
Definition of a Pressure System
A pressure system is defined in the Regulations as:
- A system comprising of one or more pressure vessels of rigid construction, together with any pipework and protective devices
- Pipework with its protective devices to which a transportable pressure receptacle can be connected
- A pipeline and its protected devices; for which any of the above contains, or is liable to contain, a relevant fluid.
A relevant 'fluid' includes steam and a fluid, or a mixture of fluids in the form of a gas with a pressure greater than 0.5 bar above atmospheric pressure. Also any liquid with a vapour pressure in equilibrium greater than 0.5 bar above atmospheric pressure at the actual temperature of the liquid, or 17.5 degrees Celsius. The Regulations also cover gas dissolved under pressure in a solvent contained in a porous substance which, would be released without applying heat.
Pressure systems include steam boilers, compressed air systems and high-pressure washing equipment, vapour compression refrigeration systems with compressor drive motors exceeding 25 kW.
The Regulations also include design, construction, installation, safe operating limits, action in case of imminent danger, operation, maintenance, modification and repair, keeping of records, precautions to prevent pressurisation of certain vessels and marking. Designers, manufacturers and suppliers must ensure that adequate information is passed on to the users about the pressure system and how it can be operated, maintained and examined safely.
Marking of pressure vessels
All pressure vessels such as air receivers manufactured in the U.K., or imported must, before being supplied be marked or have a rating plate attached to them showing:
- Manufacturer's name
- Serial number of the vessel
- Date of manufacture
- The standard to which the vessel was built
- Maximum allowable pressure
- Minimum allowable pressure where it is other than atmospheric pressure
- Design temperature.
Installation
The employer of a person who installs a pressure system at work must ensure that the installation does not give rise to danger, or otherwise impairs the operation of any protective device or inspection facility.
Repairs and modification
The employer of a person who repairs or modifies a pressure system at work must ensure that any modification or repair does not give rise to danger, or otherwise impairs the operation of any protective device or inspection facility. Any repairs or modifications carried out on a pressure system should be adequate for the duty for which the system is used, as compared with the original design specification and in accordance with appropriate standards. Consideration should be given to the possible effect of repairs or modifications on the operation of any protective devices or inspection facilities.
Safe operating limits
A pressure system should not be used unless the safe operating limits have been established with the system in use, and the safe operating limit should not be exceeded. In the case of a mobile system the owner should either supply the user, (if they are not the same person), e.g. a mobile system on hire, with a written statement specifying the safe working limits, or ensure that those limits are clearly and durably marked on the system.
This requirement does not apply to a system other than a mobile system although it is advisable to adopt it for all pressure systems.
Protective devices
Various protective devices which should be considered and incorporated, as necessary, in pressure systems are:
Steam and Pressurised Hot Water Plants:
- Suitable water drainage points and venting devices
- Safety valves, reducing valves, pressure indicating devices
- Fusible plugs
- Boiler stop-valve (not cast iron) and isolating valve
- Blow-down valves
- Controls for boilers fitted with fuel\air burners where the safety functions are controlled automatically.
Compressed Air Systems:
- Devices for indicating air pressure, oil pressure and temperature
- Fusible plugs
- Shutdown device for oil-fuelled compressors
- Safety valves and bursting discs
- Drain valves
- Vent valves.
Written scheme of examination
Requirements for a Written Scheme are:
A written scheme of examination is a document containing information about selected items of plant or equipment which form a pressure system, operate under pressure and contain a "relevant fluid". The term "relevant fluid" is defined in the Regulations and covers compressed or liquefied gas including air above 0.5 bar pressure (approximately 7 psi), pressurised hot water above 110 degrees Celsius and steam at any pressure.
Items of plant forming the pressure system should be included in a written scheme of examination if a failure of the item could unintentionally release pressure from the system, and the resulting release of stored energy could cause injury.
The following questions may help users decide on the content:
- Do the manufacturers of the plant or equipment forming the pressure system give guidance, instruction and the precautions to be taken for the safe operation of the system?
- Is pressurised plant or equipment used that requires periodic statutory examination by a recognised inspection body?
- Is any pressurised plant or equipment used that does not require periodic statutory examination by a recognised inspection body but which could fail and cause injury (e.g. by damage or corrosion)?
- Could failure of any part of the pressure system cause someone in the vicinity to be injured by the release of pressure, fragments or steam?
- Does the pressure system contain any protective devices?
If the answer to any of these questions is "Yes" then those items of plant may need to be included in the written scheme of examination.
What types of typical pressurised systems might require a written scheme of examination?
- a compressed air receiver and the associated pipework, where the product of the pressure in bars multiplied by the internal capacity in litres of the receiver is equal to or greater than 250 bar litres
- a steam sterilising autoclave and associated pipework and protective devices
- a steam boiler and associated pipework and protective devices
- a pressure cooker
- a fixed LPG storage system, supplying fuel for heating in a workplace.
The following pressurised systems are not likely to require a written scheme of examination:
- a hot water urn (for making tea)
- a pneumatic cylinder in a compressed air system
- a hand-held tool
- a combustion engine cooling system
- a portable compressed air receiver and the associated pipework, where the product of the pressure in bars multiplied by the internal capacity in litres of the receiver is less than 250 bar litres
- any pipeline and its protective devices in which the pressure does not exceed 2 bar above atmospheric pressure
- a portable fire extinguisher with a working pressure below 25 bar at 60 °C and having a total mass not exceeding 23 kilograms
- a portable LPG cylinder
- a tyre used on a vehicle.
These are typical examples for guidance purposes only. You must establish whether your pressurised system(s) is covered by the Regulations.
Responsibility of users and owners to define scope of scheme
The user of installed systems and the owner of mobile systems are responsible for deciding which pressure system is covered by the Regulations. To arrive at a properly informed decision, users or owners may seek advice from other sources. These could be Insurance Companies, in-house engineering staff, inspection bodies and consultants. However, the legal responsibility for defining the scope of the scheme rests with users or owners. The written scheme should generally cover all items within a self-contained pressurised system, which may give rise to danger. If there is more than one self-contained pressure system, there will be a need for more than one written scheme.
Confirmation of scope of scheme
When the scope of the written scheme has been decided, the user or owner of the pressure system should contact a person with sufficient knowledge and experience about the system. This person should be capable of offering informed advice on the subject. Discussions on the scope of the written scheme should be made with them, and if necessary modify the scope accordingly.
Competent person
The users or owners of pressure systems need to select a competent person and in doing so should take reasonable steps to ensure that the competent person selected can actually demonstrate competence, i.e. the necessary wealth of knowledge, experience and independence. In practice the competent person is likely to be a body or company specialising in engineering inspection work or an Insurers engineering surveyor.
Review of written scheme
The written scheme of examination must be 'suitable' throughout the lifetime of the plant or equipment and it follows that it should be reviewed, and when necessary, revised. For example, as the age of some plant increases there may be a need to carry out more frequent examinations, or change their content or type. It is the user's responsibility under the Regulations to ensure that the content of the written scheme is reviewed at appropriate intervals by a competent person to determine if it remains suitable, but clearly the competent person should be in a position to give advice on this aspect.
Legal responsibility
Users and owners of pressure systems covered by a written scheme of examination have a legal responsibility to ensure that a competent person examines the systems in accordance with the scheme.
Maintenance
The user of an installed system and the owner of a mobile system shall ensure that the system is properly maintained in good repair, so as to prevent danger.
The maintenance needs should be determined taking into account the age of the system, the conditions of operation and the environment in which it works.
Consideration should be given to what systems or parts require routine checks and replacement e.g. lubrication fluids and coolants. Some parts of systems should be subject to sample inspection during regular shutdowns when signs of deterioration, leakage, external damage or corrosion are apparent.
Pipework may not be subject to examination under the written scheme, but periodic checks should be carried out at the more vulnerable areas such as expansion loops, bends and low points.
Systems which, have been out of service, will need more detailed checks when being brought back into use.
Protective devices must be checked at appropriate intervals to ensure they remain in efficient working order. Where manufacturers/suppliers instructions are appropriate to the system and are sufficiently comprehensive they should be used to assist maintenance.
Keeping of records
The last report relating to the system made by a competent person and also any previous reports must be kept if they contain information that will help in assessing whether the system is safe to operate, or any repairs or modifications to the system can be carried out safely.
Records should also be kept of any modifications or repairs to the pressure systems.
Where the user or owner of a pressure system changes, the previous owner or user shall as soon as practicable give to the new user or owner in writing anything (relating to the system or part thereof) kept by him.
Where the Regulations require records to be kept in writing, then they can be kept in a form that is capable of being reproduced as a written copy if required. Generally records can therefore be held on computer providing they are secure from loss or unauthorised interference.
Information instruction and training
The Provision and Use of Work Equipment Regulations require that any person operating the system to be provided with adequate instructions for the safe operation of the system and the action to be taken in the event of an emergency.
The user of a pressure system shall ensure that it is not operated except in accordance with the instructions provided in respect of that system.
Instructions should include all information which operators need for safety including start up and shut down procedures, precautions needed during stand-by operation, the likely fluctuation which may occur in normal operation, the function and effect of controls and the procedures to be followed in the case of an emergency.
Such instructions should also be given as part of any training programme. It is recommended that simple concise instructions should be displayed near the relevant part of the pressure system.
Maintenance personnel should be provided with instruction to ensure proper maintenance and the detail will depend on the complexity of the system and the users organisational arrangements. For example a simple maintenance schedule could take the form of a checklist beside the system concerned.
A "competent person" must have appropriate technical expertise, theoretical and practical knowledge and experience of the pressure systems, to be able to prepare the written scheme and carry out the examinations according to the scheme. It is unlikely that most companies will have their own employees trained to the level of a competent person. Companies often employ the specialised skills of an inspection organisation or the Company’s Insurers.
Working at Height
Policy
We will, so far as is reasonably practicable, avoid the need to work at heights by the effective planning of works. Where this is not reasonably practicable we will carry out suitable and sufficient assessments of all such tasks and take appropriate steps to reduce the risk of injury. All works at height will be properly planned and appropriately supervised. The most suitable methods of work will be selected along with the most suitable work equipment. We will ensure that all employees are competent to undertake their duties and are provided with appropriate instruction, information and training. We will ensure that all equipment provided for working at height is properly maintained.
Arrangements for Working at Height
The Working at Height Co-ordinator will ensure that:
1.1 Where possible the need to work at height is eliminated.
1.2 Where work at height cannot be eliminated a risk assessment is conducted to identify suitable control measures to prevent any person from falling a distance likely to cause personal injury.
1.3 The risk assessment takes account of the distance and consequences of a fall, and the duration and frequency of the task.
1.4 Where work equipment is necessary to ensure safe working at height, the equipment is suitable for the task at hand, taking into account the risk of use, installation and removal of such equipment.
1.5 If ladders or step ladders are specified as a control measure, the assessment justifies their use, i.e. that the risk is low, the task is of short duration (15-30 minutes) or the working space/conditions dictate.
1.6 Levels of competence required for working at height activities are identified and any training needs are met.
1.7 Where identified in the risk assessment, a rescue plan is in place before work at height commences. This plan will be reviewed throughout the lifetime of the project and updated if there are any substantial changes to the work being carried out. The plan will take account of possible risks to the rescuers.
1.8 Where the activity affects or may affect others in the vicinity we will inform and discuss with these people how we plan to carry out the work.
1.9The risk assessment and planning arrangements take into account the effects that the weather can have on outdoor work at height.
1.10 The risks posed by fragile surfaces (i.e. surfaces where there is a risk of a person or object falling through, these surfaces may be either close to or part of the structure on which work is to be done and will include vertical or inclined surfaces) are managed.
1.11 Permanent fencing, guards or other permanent measures to prevent falls are put in place for work requiring regular access, including where there is a fragile surface.
1.12 Steps are taken to ensure that falling material or work equipment is prevented. Loads and equipment are stored correctly so they do not collapse or fall at any time and cause injury.
1.13 Equipment for work at height is regularly inspected to ensure that it is safe to use. The equipment is marked to ensure that it is obvious when the next inspection is due.
Pre-use checks are made before work equipment for work at height is used.
Note: The purpose of the inspection is to identify whether the equipment is fit for purpose and can be used safely and that any deterioration is detected and remedied before it results in unacceptable risks.
1.14 The provision of supervision is proportionate to the findings of the risk assessment and the experience and capability of the people involved in the work.
Guidance and Records
Falls from height are still the biggest killer on construction sites, including operation and maintenance related work, within the UK. Special consideration must be given to any work involving access ladders, stepladders, tower scaffolds, Mobile Elevating Work Platforms (MEWPs) and scaffolds.
Ladders/Stepladders
Any work at height should be carried out from or on a platform with suitable edge protection unless a specific risk assessment identifies that ladder or stepladder access alone is a safe option. Such risk assessments must be recorded and made available to all relevant operatives.
Ladders and stepladders should be of the correct type and grade, in good condition and effectively secured to prevent movement. The Health and Safety Executive (HSE) recommends EN131 Professional ladders or stepladders for use at work. EN 131 Non-professional ladders should not be available for use within the workplace.
Those who use ladders should be trained and instructed to inspect, secure and use ladders/stepladders safely. In addition, a competent suitably trained staff member should be nominated as responsible for inspecting all access equipment owned by the organisation annually and recording the results.
Mobile Access Equipment
An extensive range of mobile access equipment is available for work of short duration and minor maintenance. Such equipment may also be used to provide safe access to roofs. However mobile access equipment must be appropriate for the conditions on site, taking into account ground conditions and wind speed.
Any mobile access equipment must be adequately maintained and operated only by authorised and suitably trained staff. Where any hired equipment does not appear to be adequately maintained, it should be brought to the attention of the line manager and returned to the supplier with a report of its condition. Such equipment must not be used even in the short term.
Work on Roofs
Inspection
All roof work is dangerous, no matter how short-lived, and safe means of access and egress will be provided.
The use of alternative arrangements such as using adjacent buildings or powered access equipment must be considered when carrying out surveys on roofs that do not have safe access.
Maintenance
Many accidents occur during routine and unplanned maintenance, including cleaning, on roofs, gable ends and similar work. Fragile roofs, roof lights and the like must also be considered in the risk assessment for the job.
The cleaning of valley gutters and gutters must also be carefully considered and closely managed.
Short Duration Work
Where the risk assessment indicates that it is not reasonably practicable to install safeguards, for example for work taking minutes as opposed to hours, the assessment must be recorded before proceeding and have taken account of the following:
- Duration of the work
- Complexity of the work
- Pitch of the roof (if applicable)
- Condition of the roof (if applicable)
- Weather conditions (if applicable)
- The risk associated with providing edge protection when balanced against that without
- Any risks to others who may be affected.
Travel Restraint
Where edge protection or the use of mobile access equipment is not considered suitable, then travel restraint and fall arrest should be used.
Travel restraint is a system that does not allow the person(s) to access the edges by physically restraining them so that they cannot reach unprotected roof edges.
Note. This is not the same as fall arrest equipment, which is designed to mitigate the injuries of anyone falling.
Both travel restraint systems and fall arrest equipment must be authorised by the manager in charge of the work who should take specialist suppliers’ advice where necessary.
The risk assessment and method statement for any work requiring the use of fall arrest equipment MUST consider recovering operatives following a fall.
Training
All work at height is potentially dangerous and anyone carrying out or planning work at height, such as on roofs, or utilising access equipment will need to be suitably trained in the following as necessary:
- Erecting scaffolding, regardless of type or intricacy
- Setting up and using hoists
- Operating and checking mobile access equipment
- Rigging and inspecting safety nets, edge protection and similar
- Managers and Supervisors should be trained to be competent to:
- ensure adequate site standards
- assess and prioritise the risks associated with the work
- design safe systems of work that are appropriate to specific tasks and conditions
- prepare clear, simple safety method statements that can be used and understood by the workers involved
- recognise their own limitations and seek advice as necessary
Selecting the Right Equipment
It is important that you assess the risks and select the right equipment for the job. To assist with this requirement a Working At Height Planning checklist can be found in this policy.
Alternatively, advice and guidance can be sought from your Health and Safety Consultant.