Physical Work Environment and Equipment Safety
Housekeeping
Policy
We will ensure that standards of cleanliness and good housekeeping are maintained in all areas for which we are responsible, so as to minimise the risk of slips, trips and/or falls.
All floors and traffic routes will be maintained in good repair so as not to pose a health and safety risk to staff, other contractors and others affected by our undertakings. Employees will report any defects immediately. Traffic routes and fire escapes will be kept clear of obstructions.
Work areas will be sufficiently lit and have adequate space to enable employees to move around freely and easily.
Waste materials will be cleared up as work proceeds; debris will not be allowed to accumulate thereby presenting tripping hazards. Any spills will be removed promptly, so as to ensure floor areas are kept as clean and dry as possible.
Materials and tools will be stored correctly and areas around plant and machinery will be kept clean and free from tripping/slipping hazards. Electrical leads will be routed so as to eliminate tripping hazards, will be protected from damage and will be taken up immediately after use.
All employees will be given adequate information, instruction and training on the need for ensuring constant good safe working practices and maintained high housekeeping standards.
The necessary personal protective equipment will be provided and worn.
Arrangements for Housekeeping
The Housekeeping Co-ordinator will ensure that:
1.1 Standards of cleanliness and good housekeeping are maintained in all areas for which we are responsible.
1.2 Floors and traffic routes are maintained in good repair so as not to pose a health and safety risk to staff, other contractors and others affected by our undertakings.
1.3 Traffic routes and fire escapes will be kept clear of obstructions.
1.4 Work areas will be adequately light.
1.5 There is sufficient space to enable employees and others to move around freely and easily.
1.4 Waste materials will be cleared up as work proceeds; debris will not be allowed to accumulate and spills will be removed promptly thereby eliminating hazards.
1.5 Materials and tools, including cables and wires will be stored correctly and areas around plant and machinery will be kept clean and free from tripping/slipping hazards
1.6 All employees will be given adequate information, instruction and training on the need for ensuring constant good safe working practices and maintained high housekeeping standards.
1.7 All employees will be provided with and wear the necessary personal protective equipment, so as to minimise the risk posed by slips, trips and falls. This will include suitable safety footwear.
Guidance and Records
Organisation of Traffic Routes
‘Traffic route’ is defined as ‘a route for pedestrian traffic, vehicles or both and includes any stairs, staircase, fixed ladder, doorway, gateway, loading bay or ramp’.
There should be sufficient traffic routes, of sufficient width and headroom, to allow people on foot or in vehicles to circulate safely and without difficulty.
Features which obstruct routes should be avoided.
Cleanliness and waste
As well as regular cleaning, it is expected that cleaning should also be carried out when necessary e.g. to clear spillages, remove unexpected waste.
Cleaning should be carried out in an effective and suitable way, without exposing anyone to a health or safety risk. Care should be taken where levels of dust may lead to flammable or explosive levels, levels of wood dust may lead to inhalation etc.
Condition of floors and traffic routes
Floor and traffic routes must be well constructed, strong and stable taking into account the loads placed on them and passing over them. Floor surfaces should be free from holes, slopes, uneven or slippery surfaces that may cause a person to slip, trip or fall; cause a person to drop or lose control of something being carried; or cause instability or loss of control of vehicles and/or their loads.
Holes or bumps should be repaired, until which time barriers, guarding or markings should be used as necessary to prevent accidents.
Slopes should not be steeper than necessary and should be provided with a handrail, where needed.
Floors that are liable to get wet must not become unduly slippery, to that end slip resistant coatings should be applied where necessary. Floors near machinery should also be slip resistant and kept free from debris or slippery substances. If floors get wet regularly to the extent water can be drained off they must be provided with effective drainage e.g. laundries, kitchens etc.
Where leaks or spillages occur they should be fenced off mopped up or covered with absorbent granules immediately.
In the winter months you should make arrangements to minimise the risk posed by snow and ice, for example by clearing snow, laying grit, closing certain routes etc.
Floors and traffic routes should be kept free of obstructions, particularly near stairs, in doorways, on emergency routes etc. If temporary obstructions are unavoidable then employees should be adequately warned, for example using hazard cones.
Every open side of a staircase should be securely fenced, with at least an upper rail at 900mm or higher and a lower rail. A secure and substantial handrail should be provided and maintained on at least one side of every staircase. Additional handrails should be provided as necessary, e.g. down the middle of a wide staircase.
Falls and Falling Objects
Secure fencing should be provided where possible at any place where a person may fall 2 metres or more and where a person may fall less than 2 metres but there are factors that increase the likelihood of the fall or the risk of serious injury. Tanks/pits can be covered instead of fenced, however they must be capable of supporting loads liable to fall onto them.
Fencing should be sufficiently high and filled to prevent falls over or through, and of adequate strength to restrain persons or objects liable to fall on it. Fencing should also prevent objects falling over the edge, for example by the provision of toe boards.
With regards to work at height, scaffolding, racking etc. there is additional guidance provided in that section of the health and safety policy, if relevant to your organisation.
Control of Substances Hazardous to Health (COSHH)
Policy
We will assess the potential health effects associated with exposure to hazardous substances and take appropriate action to eliminate or adequately control them. We will regularly review and, where necessary, modify our assessments especially where there are reasons to suspect that they are no longer valid or there has been a significant change in the work to which the assessment relates. Where reasonably practicable we will eliminate the use of hazardous substances. Where this is not possible we will ensure that such substances are replaced by less hazardous alternatives. Control of exposure will be achieved by the use of appropriate safe systems of work and engineering controls and the provision of suitable work equipment and materials. Where possible, exposure will be controlled at source by using adequate ventilation and safe systems of work. The use of personal protective equipment will only be used as a control measure as a last resort and in addition to the measures described. Where required, special arrangements will be made for all work involving potential exposure to known carcinogens and biological agents. All control measures will be properly used, adequately maintained and thoroughly examined and tested as required. Where necessary for ensuring the maintenance of adequate control measures or protecting the health of staff, monitoring of workplace exposure and health surveillance will be carried out and appropriate records kept. Suitable and sufficient information, instruction and training on the findings of the assessments will be provided for all staff who are likely to be exposed to hazardous substances. Emergency plans will be produced where required.
Arrangements for the Control of Substances Hazardous to Health
The Control of Substances Hazardous to Health Co-ordinator will ensure that:
1.1 An inventory of all hazardous substances used, handled, stored or disposed of is compiled. This inventory shall include not only commercial products but also any identified exposure to dusts, fumes, etc.
1.2 Information from safety data sheets is used to assess the potential health risks for commercial products in the circumstances in which occupational exposure may occur. The potential health risks for occupational exposure to dusts, fumes, etc. shall be identified from competent reliable sources.
1.3 The results of the COSHH assessments, appropriate control measures and safe systems of work identified are communicated to the staff in a comprehensible manner.
1.4 Where possible the use of hazardous substances is eliminated, e.g. by selecting non-hazardous alternatives.
1.5 Where the elimination of a hazardous substance is not possible, every effort is made to find a less hazardous suitable alternative.
1.6 Where it is not reasonably practicable to either eliminate or substitute the use of a hazardous substance, measures are taken to control the risk of exposure by engineering means.
1.7 Staff do not bring unauthorised substances into the workplace and do not use any substance for which an assessment has not been undertaken.
1.8 Staff, and others affected, receive adequate information, instruction and training in the safe use, handling, storage and disposal of substances which they may use or encounter.
1.9 Engineering controls are examined, tested and adequately maintained at appropriate intervals to meet statutory requirements and to ensure that they continue to function effectively.
1.10 The use of personal protective equipment (PPE) is reserved as a ‘last resort’ for controlling exposure to a residual risk.
1.11 Safe working procedures are monitored to ensure that they remain effective.
1.12 Health surveillance is carried out when required.
1.13 Contractors provide evidence of suitable and sufficient assessments and adequate control measures for the control of hazardous substances whilst working on our behalf and their activities are monitored.
Guidance and Records
What is a ‘substance hazardous to health'
COSHH covers substances that are hazardous to health, which can include:
- Chemicals
- Dusts
- Fumes
- Mists
- Vapours
- Gases
- Metalworking fluids
- Flowers, bulbs, fruit and vegetables
- Wet working e.g. catering/cleaning
- Biological agents
COSHH does not cover lead, asbestos or radioactive substances as they are covered by their own legislation.
Every year, thousands of employees become ill as a result of hazardous substances. Diseases include asthma, cancer and skin disease. Employers are responsible for taking effective measures to control exposure and protect health. Ill health caused by hazardous substances is avoidable.
Substances may also be harmful as a result of them possessing other dangerous properties e.g. dust can explode if ignited, products may be flammable, etc. These hazards are covered by other regulations than the COSHH Regulations, e.g. the Dangerous Substances and Explosive Atmospheres Regulations.
Under COSHH, employers must assess the risk to their employees and then prevent or adequately control those risks). Such assessments must be documented if there are five or more employees; however it is advisable that assessments are also recorded by those with fewer employees. COSHH inventory and assessment forms can be used for this, such as those contained at the end of this guidance section.
COSHH Assessment Process
- Inventory of substances
- For a new substance/process:
- Obtain hazard data sheets from manufacturers/supplies
- Source hazard information for non-commercial substances
- Undertake preliminary assessment
- Low risk
- Ensure staff comply with precautions for use, storage, disposal etc.
- Provide PPE if required and guidance
- Medium/high risk:
- Provide PPE as interim with manufacturer’s safety measures
- Undertake in-depth assessment
- Are control measures required?
- Is specialist surveillance extraction required?
- Is specialist PPE/RPE equipment required?
- Is personal health monitoring required?
- Obtain expert advice
- Provide staff with information, instruction and training
- Plan for protection by means other than PPE
- Monitor controls, process policy and substances
- Low risk
What are control measures?
Control measures are a mixture of ways of working and equipment in order to reduce the exposure of employees and others to substances that can harm their health. No measures will work if they are not used properly. Any ‘standard operating procedure’ needs to combine the right way of working with the right equipment, which means employees must be given the right instruction, information and training.
Control measures should be chosen in order of priority:
1. Eliminate the use of the harmful substance and use a safer one
2. Use a safer form of the substance
3. Change the process to emit less of the substance
4. Enclose the process so the substance cannot escape
5. Extract emissions of the substance near source
6. Have as few workers in harm’s way as possible
7. Provide personal protective equipment (PPE) e.g. gloves, masks, etc.
Employers must make sure that control measures work properly and continue to do so. A competent person should be given the role of checking and maintaining control measures.
Examples of control measures include:
Substance | Control equipment | Way of working | Managing |
Dust/sparks from abrasive wheel. | Enclosure around the wheel.
Extract air to safe place. |
Check airflow indicator.
Ensure extraction works. |
Maintain controls. Test controls as needed by law. |
Cutting fluid mist from lathe, and Swarf. | Enclosure around the lathe.
Extract air to safe place. Efficient vacuum cleaner. |
Use skin-care products, and Ensure extraction works, and
Allow mist to clear before opening enclosure. |
Check and maintain fluid quality.
Train workers. Carry out health checks. Test controls as needed by law. |
Cleaning with solvent on rag. | Use rag holder. Provide lidded bin for rags. | Reduce vapour from used rags.
Avoid skin contact. |
Safe disposal. Check controls are in place. |
The two of the most common control measures are:
Local Exhaust Ventilation (LEV) – Such systems must be subject to checking, thorough examination and testing by a competent person. The thorough examination and testing is often done by insurance companies.
PPE – Employees who use PPE must know what they are doing. PPE must be checked and maintained because if it fails, e.g. a glove becomes ripped, it no longer provides the necessary protection.
Competence
Employers must make sure that anyone who installs maintains and tests control measures, such as an exhaust ventilation system, is competent. This means that they must have the necessary skills, knowledge and experience. As a guide, such a person should have done the work before, have relevant qualifications belong to relevant professional organisations and be able to provide good references.
Training, instruction and information for employees
Employers should involve employees in the development of control measures, so that they are suitable for how the work is actually done. Employers should also:
- Explain to employees, and others that need to know, what the dangers are
- Carry out drills for clearing spills (before spills actually occur)
- Show employees how to use control measures, and check that they are working
- Provide face fitting and training to employees who use respirators
- Show employees how to put gloves on and off without contaminating skin.
Monitoring exposure
Employers may have to monitor exposure of employees to hazardous substances, so as to ensure that they are keeping workers healthy. Such monitoring usually means air sampling but may include biological samples, e.g. breath or urine, and would be carried out after control measures have been implemented.
Monitoring usually makes reference to ‘Workplace Exposure Limits’ (WEL’s) which are published by the Health and Safety Executive (HSE) and are normally detailed on the Safety Data Sheets. The WEL is maximum limit to which employees can be exposed and must not be exceeded. The duty to prove employees are not exposed to levels above the WEL is placed on the employer.
Classification, Labelling and Packaging (CLP)
The CLP Regulations came into force on 20th January 2009 and were phased in gradually up to 2015. They ensure that the hazards presented by chemicals are clearly communicated to workers and consumers in the European Union through classification and labelling of chemicals.
Before placing chemicals on the market, industry must establish the potential risks to human health and the environment of such substances and mixtures, classifying them in line with the identified hazards. The hazardous chemicals also have to be labelled according to a standardised system so that workers and consumers know about their effects before they handle them.
It is the policy of the company to purchase chemicals with none removable or printed containers to make it difficult for labels to be removed or defaced. Decanting into smaller containers will be done as part of a COSHH risk assessment to ensure containers are correctly labelled. Labels on incoming containers of hazardous chemicals must not be removed or defaced.
These new hazard and precautionary statements (H & P phrases) for labels have replaced the existing risk and safety (R & S phrases).
New hazard statements for labels, for example:
- H240 - Heating may cause an explosion
- H320 - Causes eye irritation
- H401 - Toxic to aquatic life
New precautionary statements for labels, for example:
- P102 - Keep out of reach of children
- P271 - Use only outdoors or in well-ventilated area
- P410 - Protect from sunlight
Chemical Hazard Classification Symbols
These are the older hazard symbols that have been replaced. You may still see these on older product labels in the short term future. However, at the date of this policy these symbols are obsolete.
These are the new symbols which have replaced the older symbols completely and should now be displayed on all labels and documentation.
Other new hazard symbols unrelated to COSHH are as follows:
![]() |
![]() |
![]() |
![]() |
![]() |
Self Reactives. Organic peroxides | Oxidising gases. Liquids and solids | Flammable gases, aerosols, liquids or solids | Compressed gasses | Hazardous to the Aquatic environment |
Electrical Safety
Policy
We will ensure that all electrical systems and equipment are provided and maintained in a safe condition. All work on or near electrical systems will be carried out in a safe manner and all equipment provided for protecting employees working on or near electrical equipment will be suitable for such use and adequately maintained. All electrical equipment will be of sufficient strength and capability for its intended use and of such construction or adequately protected to prevent danger arising from the conditions of its use. All electrical equipment will be suitably insulated and protected to prevent danger. Arrangements for earthing and ensuring the integrity of referenced conductors will be made. All electrical connections will be mechanically and electrically safe. Suitable means for protecting electrical circuits from excess current and the isolation of equipment will be provided and maintained. Work on electrical systems will only be carried out by Competent Persons. Safe systems of work will be followed at all times. Live working will be subject to a Permit to Work system and only be allowed where the criteria described in the Electricity at Work Regulations are met. Safe access and adequate lighting will be provided to enable work on electrical systems to be performed safely. All portable electrical equipment will be maintained in a safe condition and inspected and tested regularly.
Arrangements for Electrical Safety
The Electricity at Work Co-ordinator will ensure that:
1.1 The fixed mains installation is installed, inspected and tested periodically by a competent person in accordance with the IET Wiring Regulations 18th Edition.
1.2 Suitable means for isolating electrical equipment, including the identification of individual circuits, are provided and maintained.
1.3 Work on electrical systems is only carried out by Competent Persons following safe systems.
1.4 Live working is not carried out unless a Permit to Work system is in place and the criteria in the Electricity at Work Regulations are met.
1.5 Safe access is provided for competent persons (both in-house and external) maintaining electrical systems or work equipment.
1.6 An inventory of portable electrical equipment is compiled covering all workplaces and equipment under our control, including employee owned equipment where its use has been authorised.
1.7 Portable electrical equipment is inspected for safety prior to first issue.
1.8 Routine combined inspection and testing is undertaken at intervals recommended by a competent person according to the type of use.
1.9 Employees are instructed in safe systems of work and carry out simple checks of equipment prior to each use for visible defects and damage.
1.10 More detailed formal inspections by a responsible person are undertaken to supplement the visual checks, at frequencies determined by assessment.
1.11 A procedure is in place to report damaged or defective equipment and that such equipment is removed from service immediately by the person discovering the fault.
1.12 Employees are instructed to report damaged or defective equipment or dangerous conditions.
1.13 Contractors using electrical equipment in a workplace under our control provide evidence of its safety prior to commencement of work.
1.14 Privately owned electrical equipment is not used in the workplace without authorisation from management, its safety being confirmed, an entry made on the inventory and it being included in the inspection and testing programme.
Guidance and Records
Procedures for Inspection and Testing
The suitability of electrical equipment for its intended purpose will be determined through risk assessment. All equipment will be entered onto the inventory and the inspection and testing programme. The different types of inspection and testing we will carry out are outlined below.
User Checks
Employees will be instructed to carry out simple visual pre-use checks for damage to the outside of the equipment and its lead and plug, but without taking the plug apart. Sockets will also be checked for signs of damage and burn marks.
Formal Visual Inspections:
These include the pre-use visual checks but also include checking within the plug top. A responsible authorised person will undertake this but will not remove covers of the actual equipment or attempt repair, unless competent to do so. They will however, take faulty equipment out of service and affix a warning sign and prevent further use.
Combined Inspections and Repair
Some faults cannot be detected through visual inspection, particularly lack of continuous earths. For some equipment the earth is essential to safety and therefore all earthed equipment, leads and plugs connected to it, will also have occasional combined inspection and testing.
This will be carried out:
- Where there is reason to suspect the equipment may be defective, but this cannot be confirmed by a visual inspection
- After any repair, modification or similar work
- At periods appropriate to the equipment, the manner and frequency of use and the environment.
A competent employee may undertake this where the item to be tested is plugged into a simple Fail/Pass portable appliance test (PAT) meter, or alternatively an external competent person will be employed. Where our own employee undertakes this task clear, easy to follow guidance will be given and, if an employee with limited skills is undertaking the testing they will only be required to report the fault for subsequent correction by a ‘professional.’ All other test equipment, which gives a reading and requires interpretation will only be used by an appropriately qualified person.
Recommended Minimum Frequency of Inspection and Testing:
The following type and initial intervals of inspections/tests are recommended in low risk environments:
Equipment | Operator Checks | Formal visual inspection | Combined inspection & test |
Battery operated less than 20 volts | NO | NO | NO |
Extra low voltage:
Less than 50 volts e.g. telephone, low voltage desk lights |
NO | NO | NO |
Information technology; Computers, screens | NO | Yes
2 - 4 years |
Not if double insulated
Otherwise up to 5 years |
Photocopiers, fax, rarely moved, NOT hand-held items | NO | Yes
2 - 4 years |
Not if double-insulated
Otherwise up to 5 years |
Double insulated:
NOT hand-held. e.g. fans, table lamps, projectors |
NO | Yes
2 - 4 years |
NO |
Double insulated:
HAND-HELD e.g. some floor cleaners |
YES | Yes
6 months - 1 year |
NO |
Earthed equipment (class 1)
e.g. kettles, some floor cleaners |
YES | Yes
6 months - 1 year |
Yes 1 - 2 years |
Cables (leads) and plugs connected to the above
|
YES | Yes
6 months - 4 years depending on type of equipment it is connected to |
Yes 1 - 5 years depending on type of equipment it is connected to |
Special, frequent testing and arrangements are required for high risk equipment used in more aggressive environments.
Portable Electrical Appliances in Low-Risk Environments: Operator Pre-Use Checks
Operators are to check for damage to the outside of the equipment and its lead and plug before they use it but must not take the plug apart.
The plug must be disconnected from the mains supply and the following checked.
Mains lead/Cable covering | There should be no cuts or abrasion (light scuffing is acceptable).
Report any non-standard joints, including taped joints. |
Cable grip | The cable should not be loose where it enters the plug.
The coloured insulation of the internal wires should not be visible where the cable enters the plug. |
Plug | The casing must not be cracked or loose.
The pins must not be bent. Check for signs of overheating - burn marks. |
Damage to outer cover/casing | This should be undamaged.
Check for cracked casing, obvious loose parts, screws etc. Signs of overheating - burn marks. |
Mains on/off switch Sockets | It should be tight to the wall not loose.
Does it operate correctly/as expected? Is it cracked? Are there burn marks? |
Formal Visual Inspection
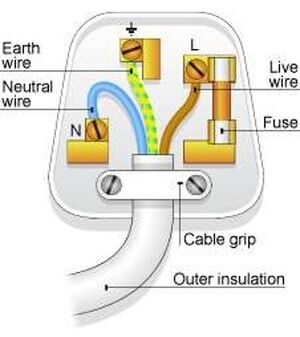
Formal inspection involves all of the operator checks plus removing the plug cover to check the following:
Fuse: | a proper fuse not a piece of wire, nail etc. |
Cord grip: | should hold the outer part (sheath) of the cable tightly. |
Wires: | attached to correct terminals with no bare wire visible other than at terminals. |
Terminal screws: | must be tight. |
Internal damage: | check for signs of overheating, or entry of liquid, dust or dirt. |
Electrical Installation testing
All fixed electrical installations should be inspected and tested periodically, which includes the wiring to machinery and earth bonding. The frequency of this inspection and testing will depend on the Companies operations and activities, for example in commercial premises the maximum period between inspections is 5 years, whilst in industrial premises that period is 3 years. Further guidance on this can be obtained from competent electrical contractors or consultants.
This period inspection will:
- Reveal if electrical circuits or equipment are overloaded.
- Identify defective electrics.
- Highlight the lack of earth or bonding.
- Identify potential electric shock risks or fire hazards.
The fixed installation inspection and testing should be carried out by a competent person, such as a contractor who has been approved by one of the following:
- National Inspection Council for Electrical Installation Contracting (NICEIC)
- National Association for Professional Inspectors and Testers (NAPIT)
- Electrical Contractors Association (ECA)
- The Electrical Contractors Association of Scotland (SELECT)
An Electrical Installation Condition Report, commonly known as a Periodic Inspection Report should be provided by the competent contractor showing full details of the examination and tests carried out. This certificate should be held on file for reference and examination.
This report may identify the electrical installation as being ‘unsatisfactory’ if potentially dangerous or dangerous conditions are found. In such circumstances remedial action must be taken without delay to remedy the defects.
Any part of an installation that has been damaged or is identified as defective between the periodic inspection and test should be de-energised until the problem can be rectified. Any such minor works should be accompanied by a certificate, which should be kept on file.
It is possible to carry out simple in house checks on the electrical installation using a socket tester, however many types of socket testers cannot detect certain types of fault and could show the socket is safe when it is not.
Provision and Use of Work Equipment (PUWER)
Policy
We will ensure that all work equipment is suitable for the purpose for which it is to be used, is installed correctly and inspected and maintained in good working order.
Where the use of work equipment is likely to involve a specific risk to health and safety we will ensure that the equipment is only used, repaired, modified maintained and serviced by authorised competent persons. Appropriate health and safety information, instruction and training will be provided for all employees who either use or manage the use of work equipment.
We will ensure that all work equipment provided for use after 31st December 1992 complies with the appropriate EU directives. We will also ensure all work equipment complies with UK legislation. Access to dangerous parts of machinery will be effectively prevented by the provision of suitable guards or protective devices that are of good construction, sound material, adequate strength and effectively maintained.
We will take all necessary measures to prevent, or where this is not practicable, adequately control exposure to specified hazards associated with the use of work equipment.
We will ensure that all machinery is provided with suitable controls and control systems for starting, stopping and changing operating conditions, including those for use in an emergency situation. Where appropriate all machinery will be provided with suitable means to isolate it from its sources of energy. All work equipment will be stable, adequately lit, clearly marked for reasons of health and safety and incorporate appropriate warnings or warning devices. Maintenance of work equipment will only be carried out where suitable measures have been taken to effectively control the risks.
LEGAL DEFINITION:
“Work Equipment” means any machinery, appliance, apparatus, tool or installation for use at work (whether exclusively or not).
PUWER applies to the provision and use of all work equipment, including mobile and lifting equipment.
Arrangements for the Provision and Use of Work Equipment
The Provision and Use of Work Equipment Co-ordinator will ensure that:
1.1 All work equipment is suitable for the purpose for which it is to be used and is maintained in good working order and where necessary an up-to-date maintenance log is available.
1.2 All work equipment is installed correctly and is inspected at suitable intervals to ensure it remains safe and that appropriate records of inspection are maintained.
1.3 Where the use of work equipment is likely to involve a specific risk to health and safety the equipment is only used, repaired, modified, maintained and serviced by authorised competent persons.
1.4 Appropriate health and safety information, instruction and training is provided for all employees who either use or manage the use of work equipment.
1.5 All work equipment provided for use after 31st December 1992 complies with the appropriate EU directives and be CE marked. From January 2021 the UKCA mark will start to replace the CE mark for goods sold within Great Britain. The CE mark will continue to be required for goods sold in Northern Ireland.
1.6 Access to dangerous parts of work equipment is effectively prevented by the provision of suitable guards or protective devices that are of good construction, sound material, adequate strength and effectively maintained.
1.7 All necessary measures are taken to prevent, or where this is not possible, adequately control exposure to specified hazards associated with the use of work equipment and to prevent contact with surfaces that are at either very high or very low temperatures.
1.8 Where appropriate, all work equipment is provided with suitable controls and control systems for starting, stopping and changing operating conditions, including those for use in an emergency situation.
1.9 Where appropriate all work equipment is provided with suitable means to isolate it from its sources of energy.
1.10 All work equipment is stable, adequately lit, clearly marked for reasons of health and safety and incorporates appropriate warnings or warning devices.
1.11 Maintenance of work equipment is only to be carried out where suitable measures have been taken to effectively control the risks.
Guidance and Records
Introduction
You are required to ensure that all work equipment is safe and appropriate for use. This can be achieved via the risk assessment process required by the Management Regulations. You must ensure that work equipment is properly maintained, serviced, repaired or modified safely and where the use of work equipment is likely to involve a specific risk to the health and safety of any person, you must restrict its use to those trained to use it. All persons using work equipment must be given adequate health and safety information and, where appropriate, written instructions. You must ensure that those employees who use work equipment and those supervising or managing such use, receive adequate training, on the risks they are exposed to and the precautions to be taken to control those risks.
Guards
You must ensure that effective measures are taken to prevent access to dangerous parts of machinery or to stop the machinery before people can reach the dangerous parts. This should be done by the provision of guards or protective devices, so far as is practicable. All guards or protective devices must: be appropriate for the purpose for which they are provided, well constructed, of sound material, adequate strength and be free from patent defect. They must be properly maintained, not create additional risks in themselves, not be easily removed or rendered inoperative, be situated a sufficient distance from the danger area, not restrict - more than necessary - any view of the operation of the work equipment, and allow operators to fit or replace parts without, if possible, removing the guards or protection devices.
Risks to Health & Safety
You should so far as is reasonably practicable, ensure protection against risks to health or safety as a result of any failure in the work equipment. This protection should be secured, so far as is reasonably practicable, by measures other than personal protective equipment. In this context failure can include ejected or falling objects, rupture or disintegration of parts of the equipment; fire or overheating, the unintended or premature discharge or ejection of any article, gas, dust, liquid, vapour or other substance which is produced, used or stored in the equipment; or the unintended or premature explosion of the equipment or of any material produced, used or stored in it. You must also ensure that workers are prevented from coming into contact with parts of work equipment and material produced, used or stored in it which is at a temperature likely to cause injury by burning, scalding or searing.
Controls
You must ensure that, where appropriate, work equipment is provided with one or more controls to start the equipment (including restarting after any stoppage) or change the speed, pressure or other operating conditions. You must also ensure that, where appropriate, work equipment is provided with one or more controls which, when operated, will bring the work equipment to 'a safer condition in a safe manner'.
This would normally bring the work equipment to a stop, unless it would be unsafe to do so. The operation of such controls should not depend on sustained manual action and, if necessary, should disconnect all sources of energy after stopping the work equipment. These controls should operate in priority to any control that starts or changes the operating conditions of the work equipment.
Emergency stop controls must be provided unless the nature of the hazards deems them unnecessary. All emergency stops must operate in priority over those control systems previously identified. All controls of work equipment must be clearly visible and identifiable, including appropriate marking, where necessary.
No controls should be in a danger area except where it cannot be avoided. It should not be possible, so far as is reasonably practicable, to operate any control from within a danger area that initiates mechanisms in that area. Where this is not possible, safe systems of work should be applied to ensure that no one is in the danger area, when work equipment is started. If it is not reasonably practicable to apply either of these measures an audible or visible warning must be given whenever work equipment is about to start. You must also ensure that any workers wholly or partly in a danger zone are able to avoid any hazard caused by the starting or stopping of work equipment.
You must ensure that all control systems of work equipment are safe, so far as is reasonably practicable. Such control systems are not considered safe unless they ensure, so far as is reasonably practicable, that any failure in the system cannot result in additional or increased risk to health and safety; and prevents so far as is reasonably practicable, the equipment being started or restarted while any person is in the danger zone and does not impede any emergency stop controls.
Isolation
You must ensure that work equipment is provided with appropriate means to isolate the equipment from all its sources of energy. Such means must be clearly identifiable, readily accessible and include ways of preventing risks to health and safety of any person from any part of the work equipment which is liable to fail.
Stabilisation
You must ensure that work equipment, or any part of work equipment, is stabilised by clamping or otherwise where necessary for the purposes of health and safety and that any place where a person uses work equipment is adequately lit by appropriate means and in line with the operations to be carried out.
Maintenance Operations
You must ensure that, so far as is reasonably practicable, maintenance operations on work equipment can be done while the work equipment is stopped. If not, either the maintenance operations can be done without anyone entering the danger zone, or appropriate measures are taken to protect anyone when they are carrying out maintenance operations on work equipment.
CE Mark/Transition to UKCA Mark
You must ensure that work equipment is uniquely marked to aid its identification for maintenance etc.
All work equipment provided for use after 31st December 1992 should carry the CE Mark to confirm its compliance with all appropriate UK and European legislation i.e.
You must also ensure that work equipment incorporates any warnings or warning devices which are appropriate for the purposes of health and safety. Such warnings or warning devices must be unambiguous, easily perceived and easily understood.
As the UK is no longer part of the European Union, new rules apply to marking all equipment previously subject to CE marking. To allow business time to adjust the CE mark can still be used until 11pm on 31st December 2022. After this date, the government is intending to introduce legislation to allow extra easement time until 11pm on 31st December 2025. This will allow business to affix a label to a product or documentation accompanying a product. This label will display the new UKCA mark.
If products are to be sold in Northern Ireland or EU, the UKCA mark cannot be used.
Rules for using the UKCA image
You must make sure that:
- if you reduce or enlarge the size of your marking, the letters forming the UKCA marking must be in proportion to the version set out below
- the UKCA marking is at least 5mm in height unless a different minimum dimension is specified in the relevant legislation
- the UKCA marking is easily visible, legible and indelible
Mobile work equipment
Measures must be taken to protect employees carried on mobile work equipment where there are risks from roll-over whilst it is travelling. Examples are dumper trucks on construction sites or any vehicles working on slopes. Equipment such as excavators, or a vehicle with a winch when operating in a stationary position, are not included. However, this is covered by Regulation 20, which relates to stability. This again links directly to the risk assessment requirements of the Management Regulations.
Roll-over protective structures (ROPS)
ROPs are normally fitted on mobile work equipment which is at risk from 180 degree, or more, rollover. They may be structures, cabs or frames which, in the event of as rollover, prevent the work equipment from crushing persons being carried by it.
Before fitting ROPS to older work equipment, which has no anchorage points fitted on it (in use before December 5th 1998), an engineering analysis will be necessary.
Restraining Systems
You should provide the above (e.g. seat belt) where appropriate, if they can be fitted to the equipment (e.g. forklift truck) to prevent persons being carried from being crushed between the truck and the ground, should it overturn.
Control of Dangerous Substances and Explosive Atmospheres (DSEAR)
Policy
We recognise the continual risk of fire, explosions and similar events in the workplace, this includes risks to members of the public from the work activity in our premises, whether caused by accident or by malicious intent.
We will reduce the quantity of dangerous substances in our premises, to a minimum. We will undertake a risk assessment to ensure we:
- Identify what dangerous substances are in the workplace and what the fire and explosion risks are.
- Have adequate control measures in place to avoid or minimise the release of substances.
- Prevent the formation of an explosive atmosphere and reduce the effects of any incidents involving dangerous substances.
- Prepare plans and procedures to deal with accidents, incidents and emergencies involving dangerous substances.
- Have properly informed and trained our employees to control or deal with the risks from the dangerous substances.
- Have identified and classified the areas of the workplace where explosive atmospheres may occur and ignition sources (from unprotected equipment, for example) are avoided in those areas.
- Keep incompatible substances apart.
Arrangements for the Control of Dangerous Substances and Explosive Atmospheres
The Dangerous Substances and Explosive Atmospheres Co-ordinator will ensure that:
1.1 A risk assessment is conducted and appropriate measures to reduce the risks are implemented.
1.2 The quantity of dangerous substances is kept to a minimum
1.3 The release of a dangerous substance is minimised or avoided.
1.4 The release of a dangerous substance is controlled at source.
1.5 The formation of a dangerous substance is prevented.
1.6 Any release of a dangerous substance will be collected, contained and removed to a safe place (for example through ventilation).
1.7 Ignition sources are avoided.
1.8 Adverse conditions are avoided (for example exceeding the limits of temperature or control settings) that could lead to danger.
1.9 Incompatible substances are kept apart.
1.10 The number of employees exposed to the risk is kept to a minimum.
1.11 Plant that is provided is explosion resistant
1.12 Explosion suppression or explosion relief equipment is provided.
1.13 Measures are taken to control or minimise the spread of fires or explosions.
1.14 Suitable personal protective equipment (ppe) is provided.
1.15 The areas where potentially explosive atmospheres may occur are identified and classed (zoning).
1.16 Ignition sources are avoided in zoned areas.
1.17 Where necessary the entrances to zoned areas are identified.
1.18 Before they come into operation, for the first time, areas where explosive atmospheres may be present are confirmed as being safe by a competent person.
1.19 Employees are trained and instructed on relevant policies and procedures.
1.20 Visitors to the premises are made aware of rules and procedures.
1.21 Contractors are informed of policy and procedures and asked for information on how they intend to control any hazard associated with their work.
Guidance and Records
Introduction
The Dangerous Substances and Explosive Atmospheres Regulations 2002 (DSEAR) impose requirements for eliminating or reducing risks to safety from fire, explosion or other events arising from the hazardous properties of dangerous substances in connection with work.
Dangerous substances include substances or preparations (including dust) that are explosive, oxidising, extremely flammable, highly flammable or flammable, or can form an explosive mixture with air.
Employers are required to carry out a suitable and sufficient assessment of the risks where dangerous substances may be present in the workplace. The Management of Health and Safety at Work Regulations already require a risk assessment be undertaken but where a dangerous substance is or may be present there is a specific requirement to assess the risk from dangerous substances under these Regulations.
Places where explosive atmospheres may occur must be classified as hazardous or non-hazardous and hazardous places must be classified into zones on the basis of the frequency and duration of the explosive atmosphere.
As with all regulations, some activities and processes are exempt from some of the requirements.
Specific activity related guidance, supplementing the key requirements set out in this document, has been included as appendices as follows:
Appendix A: | Design of plant, equipment and workplaces |
Appendix B: | Storage of dangerous substances |
Appendix C: | Control and mitigation measures |
Appendix D: | Safe maintenance, repair and cleaning procedures |
Risk Assessment
Under these Regulations no new work activity involving a dangerous substance shall commence unless an assessment has been made and control measures implemented. The risk assessment shall include consideration of:
- the hazardous properties of the substance
- information provided by the supplier
- the work processes and substances used and possible interactions
- the amount of substance involved
- where the work involves more than one dangerous substance, the risk presented by such substances in combination
- the arrangements for the safe handling, storage and transport of dangerous substances and of waste containing dangerous substances
- activities, such as maintenance, where there is potential for a high level of risk activities
- the effect of measures taken
- the likelihood that an explosive atmosphere will occur and its persistence
- the likelihood that ignition sources, including electrostatic discharges, will be present and become active and effective
- the scale of the anticipated effects of a fire or an explosion
- any places which are or can be connected via openings to places in which explosive atmospheres may occur
- such additional safety information as may be needed in order to complete the risk assessment
Elimination or reduction of risks
The regulations require that risk is either eliminated or reduced so far as reasonably practicable. The first consideration must be to avoid the presence or use of dangerous substances but where this is not reasonably practicable risks need to be controlled and action taken to mitigate the detrimental effects arising from dangerous substances. This may be achieved by:
- reducing the quantity of dangerous substances to a minimum
- avoiding or minimising the release of dangerous substances
- controlling the release of a dangerous substance at source
- preventing the formation of an explosive atmosphere
- ensuring released dangerous substances which may present a risk is
- collected, contained and removed to a safe place, or otherwise made safe
- avoiding sources of ignition, including electrostatic discharges, and adverse conditions which could cause dangerous substances to give rise to harmful effects
- segregating incompatible dangerous substances
Mitigating detrimental effects
Detrimental effects may be mitigated by:
- reducing to a minimum the number of employees exposed
- avoiding the propagation of fires or explosions
- providing explosion relief and suppression systems
- providing plant which is constructed to withstand explosion
- providing suitable personal protective equipment for employees
General safety measures
The following measures are specified in Regulations for the employer to take if appropriate:
Workplace and work processes:
- ensuring that the workplace is designed, constructed and maintained so as to reduce risk
- designing, constructing, assembling, installing, providing and using suitable work processes so as to reduce risk
- maintaining work processes in an efficient state, in efficient working order and in good repair
- ensuring that equipment and protective systems meet the following requirements:
- where power failure can give rise to the spread of additional risk, equipment and protective systems must be able to be maintained in a safe state of operation independently of the rest of the plant in the event of power failure
- means for manual override must be possible, operated by employees competent to do so, for shutting down equipment and protective systems incorporated within automatic processes which deviate from the intended operating conditions, provided that the provision or use of such means does not compromise safety
- on operation of emergency shutdown, accumulated energy must be dissipated as quickly and as safely as possible or isolated so that it no longer constitutes a hazard
- necessary measures must be taken to prevent confusion between connecting devices
Organisational measures
The application of appropriate systems of work including:
- the issuing of written instructions for the carrying out of the work
- a system of permits to work with such permits being issued by a person with responsibility for this function prior to the commencement of the work
Places where explosive atmospheres may occur
A place where an explosive atmosphere may occur to such an extent as to require special precautions to protect the health and safety of the workers concerned is deemed to be “hazardous” within the meaning of the regulations.
A place in which an explosive atmosphere is not expected to occur to such an extent as to require special precautions is deemed to be “non-hazardous” within the meaning of the regulations.
Hazardous places are classified in terms of zones on the basis of the frequency and duration of the occurrence of an explosive atmosphere.
Zone 0: A place in which an explosive atmosphere consisting of a mixture with air of dangerous substances in the form of gas, vapour or mist is present continuously or for long periods or frequently.
Zone 1: A place in which an explosive atmosphere consisting of a mixture with air of dangerous substances in the form of gas, vapour or mist is likely to occur in normal operation occasionally.
Zone 2: A place in which an explosive atmosphere consisting of a mixture with air of dangerous substances in the form of gas, vapour or mist is not likely to occur in normal operation but, if it does occur, will persist for a short period only.
Zone 20: A place in which an explosive atmosphere in the form of a cloud of combustible dust in air is present continuously, or for long periods or frequently.
Zone 21: A place in which an explosive atmosphere in the form of a cloud of combustible dust in air is likely to occur in normal operation occasionally.
Zone 22: A place in which an explosive atmosphere in the form of a cloud of combustible dust in air is not likely to occur in normal operation but, if it does occur, will persist for a short period only.
It should be noted that layers, deposits and heaps of combustible dust must be considered as a source which can form an explosive atmosphere.
Criteria for the selection of equipment and protective systems
Equipment and protective systems for all places in which explosive atmospheres may occur must be selected on the basis of the requirements set out in the Equipment and Protective Systems Intended for Use in Potentially Explosive Atmospheres Regulations 1996 unless the risk assessment finds otherwise. In particular, the following categories of equipment must be used in the zones indicated, provided they are suitable for gases, vapours, mists, dusts or mists and dusts, as appropriate:
- zone 0 or zone 20 – category 1 equipment
- zone 1 or zone 21 – category 1 or 2 equipment
- zone 2 or zone 22 – category 1, 2 or 3 equipment
These requirements shall not apply to equipment and protective systems for use in places where explosive atmospheres may occur which are or have been in the workplace on or before 30th June, 2003.
Warning signs
The triangular warning sign illustrated below, having black letters on a yellow background with black edging, should be displayed at points of entry to places classified as hazardous.
Additionally all containers and pipes used for dangerous substances shall be clearly marked to show the contents and associated hazards.
Verification by competent person
Before a workplace classified as hazardous is used for the first time the employer shall ensure that its overall explosion safety is verified by a person competent in the field of explosion protection.
Work clothing
The employer shall ensure employees working in places classified as hazardous are provided with work clothing which does not give rise to electrostatic discharges.
Accidents, incidents and emergencies
Procedures shall be prepared, which include first-aid arrangements and safety drills, in order to protect the safety of employees. The emergency arrangements shall also include information for employees on the relevant hazards, hazard identification arrangements and the specific hazards likely to arise at the time of any incident.
The arrangements shall also ensure that:
- suitable warning and other communication systems are available to initiate an appropriate response including rescue operations
- where necessary, before explosion conditions are reached, appropriate warnings are given and employees withdrawn
- where necessary, escape facilities are provided and maintained
The information on dealing with incidents shall be displayed in the workplace and provided to the emergency services to enable them to prepare their own procedures.
Information, instruction and training
Employees shall be provided with suitable and sufficient information, instruction and training on the precautions and action to be taken including:
- the name of the substance and the risk
- access to relevant safety data sheet
- legislative provisions relevant to the hazardous properties of the substance
- the significant findings of the risk assessment
APPENDIX A: Design of Plant, Equipment and Workplaces
APPENDIX B: Storage of Dangerous Substances
APPENDIX C: Control of Mitigation Measures
APPENDIX D: Safe Maintenance, Repair and Cleaning Procedures
Display Screen Equipment
Policy
We will ensure that the risks to the health and safety of our employees from the use of display screen equipment are adequately controlled. All users will be identified and workstations assessed to ensure that they meet the requirements of the Regulations. All users will take regular breaks or changes in activity to reduce their workload at display screen equipment. Eye and eyesight tests by a competent person will be provided for all users at their request and will be repeated at regular intervals. Where the results of such a test show that the user needs special corrective appliances when using display screen equipment, we will ensure that they are provided. Training and information on the use of display screen equipment, the findings of the workstation assessment, the health risks from display screen equipment, the measures taken to reduce the risks, the need to plan the work routine and to take regular short breaks and the availability of eye and eyesight tests will be provided for all users. Training will also include reference to the organisational arrangements for reporting medical symptoms or problems with equipment to management.
Arrangements for Display Screen Equipment (DSE) Safety
The Display Screen Equipment Co-ordinator will ensure that:
1.1 A comprehensive assessment of each workstation is undertaken as required by the DSE Regulations.
1.2 Appropriate action to correct any risks highlighted as a result of the assessment are implemented.
1.3 Where appropriate, work routines will be modified to prevent intensive periods of DSE activity.
1.4 Software is suitable for the task and is not unnecessarily complicated.
1.5 Employees using DSE are informed of their entitlement to eye and eyesight tests and that procedures are in place for employees to avail themselves of such tests.
1.6 Where required specifically for working with display screen equipment, the provision of special corrective spectacles at the company’s expense.
1.7 Employees working or intending to work with display screen equipment are advised on the associated risks to health and how these are to be avoided.
1.8 Adequate information, instruction and training on all aspects of DSE work is provided.
Guidance and Records
Definitions
In the Health and Safety (Display Screen Equipment) Regulations the following phrases or words have been defined:
“Display screen equipment” is any alphanumerical or graphic display screen, regardless of the display process involved. This includes computers and portable display screen equipment that is in prolonged use e.g. laptops.
“Operator” is a self employed person who habitually uses display screen equipment as a significant part of his normal work.
“Use “ is use for or in connection with work.
“User” is an employee who habitually uses display screen equipment as a significant part of his normal work. This will include agency workers.
“Workstation” is an assembly comprising of display screen equipment; any optional accessories; disk drive, telephone, modem, printer or other item peripheral to the display screen equipment; and the immediate work environment around the display screen equipment.
Who is a user?
The Regulations cover employees who are users whether they are working at a workstation at your premises, at a workstation from home or at another employers workstation. Self employed persons are also covered if they work at an employers workstation and their use of display screen equipment (DSE) means they would be users if they were employed.
Employers must decide which of their employees are users. Health and Safety Executive guidance (HSE) states that it would usually be correct to classify an employee as a user if they:
- Normally use DSE for continuous or near continuous spells of an hour or more at a time; and
- use DSE in this way more or less daily: and
- have to transfer information quickly to or from the DSE;
And also need to:
- apply high levels of concentration and attention; or
- are highly dependent on DSE; or
- have little choice about using it; or
- need special training; or
- skills to use the DSE.
Please note the use of the words ‘and’ and ‘or’ in the above definition.
This definition applies equally to full time and part time staff.
Some examples of definite display screen equipment users are:
- Word processing worker
- Secretary
- Typist
- Date input operator
- Journalist
- Telesales/customer complaints/accounts enquiry
- Television editing technician
- Security control room operative
- Air traffic controller
- Graphic designer.
Further guidance on whether employees are users or not can be found on the HSE’s website or from consultants.
Homeworkers
If a DSE user works at home, or elsewhere then the Regulations still apply. Such workers will be exposed to the usual risks associated with DSE, and some potentially increased risks such as social isolation, stress, lack of supervision etc. It is not always practical for an employer to send someone to carry out a risk assessment for home workers, so it would be adequate to train them to carry out their own assessment. Homeworkers may require additional training and information about health and safety as they will not be under immediate supervision and may pick up bad habits.
Agency Workers
When a DSE worker is supplied by an agency and becomes an employee then the host employer must meet all the requirements laid down in the DSE regulations. If however, the DSE worker is still employed by the agency or is self employed then agency and host employer both have duties under the regulations. The majority of the duties fall to the host employer however the agency should:
- Provide eye tests on request (and special corrective glasses if necessary)
- Provide health and safety training including information about eye tests
- Check the host employers carry out their duties.
Risks associated with DSE use
The main risks associated with DSE work are physical (musculoskeletal) problems, mental stress and visual fatigue. The risks to users should be low, assuming the requirements of the regulations are met and ergonomic principles are followed with regard to the equipment; design of the workplace and organisation of the task.
More information about the risks is outlined below:
- Musculoskeletal disorders – This can include upper limb disorders/work related upper limb disorders e.g. carpal tunnel syndrome, temporary fatigue, soreness etc. It can also include back pain (existing or new)
- Fatigue and stress – Several factors can contribute to fatigue and stress in DSE employees and should be avoided. These factors are similar to those that have been linked to stress at work and include little or lack of control over work, not using all of skills, not being involved in decisions that affect users, work being system paced, payment systems that encourage fast work or insufficient breaks, high levels of effort not balanced by reward, etc.
- Eye and eyesight effects – Using DSE is not associated with permanent damage to eyes or eyesight, however some employees may get temporary visual fatigue which may lead to blurred vision, red or sore eyes, headaches, adoption of awkward posture. Such symptoms may be caused by being in the same position too long; poor position of the DSE; poor legibility of the screen, documents or keyboard; poor lighting or poor image on the screen. Uncorrected defects can lead to DSE work being more tiring or stressful than is necessary
- Epilepsy – Work with DSE has been linked to epileptic seizures, however this is very rare
- Facial dermatitis – Facial skin complaints, such as itching and reddened skin on face or neck are rare and there is limited evidence linking them to DSE use
- Electromagnetic radiation – levels of ionising and non-ionising radiation generated by DSE are well below international recommendations and the National Radiological Protection Board does not consider such levels pose a significant risk to health. In addition, there is no scientifically proven link between miscarriages/birth defects and working with DSE.
Information and training
Employers will need to arrange training for DSE Users, which should cover:
- The risks from DSE work
- Importance of good posture
- How to adjust furniture to avoid risks
- How to organise the workplace to avoid awkward or repeated stretching movements
- Avoiding glare and reflections on the screen
- Adjusting and cleaning the screen
- Adjusting and cleaning the mouse
- Organising work so there are activity changes and breaks
- Who to contact for help or report problems
- Contributing/completing risk assessments and checklists.
This training can be done using videos, computer based training, wall charts, tool box talks, seminars or the HSE working with VDU booklet.
Employers also need to arrange training for workstation assessors, which should cover:
- How to review checklists
- How to identify hazards (obvious and less obvious)
- Deciding when more information is required, and where to find it
- Reviewing and drawing conclusions from assessments and identify steps to reduce risks
- Recording problems
- How to tell those who need to act on findings and give users the feedback they need.
This training can be done at professionally arranged sessions/seminars, computer based training or reading HSE’s DSE work: Guidance on Regulations.
All training should include assessments, to ensure information has been absorbed, and should be fully documented.
The HSE guidance information referred to above can be found www.hse.gov.uk
Workstation assessment
The workstations of DSE users can be assessed using a checklist, such as the one contained at the end of this guidance. It is important to remember that the user filling in the assessment is only one stage of the process, in that a trained assessor needs to go over the checklist to identify problems, provide solutions, clarify matters etc.
Workstation assessments should be reviewed;
- Where there is a significant change to the workstation, for example if a new screen is provided
- If the workstation is relocated
- If new users start work
- If the nature of the work changes considerably.
Breaks/Changes of routine
Employers should aim to break up long spells of DSE work with other work e.g. filing, telephone calls, so as to reduce the risk of fatigue, backache, eye strain etc. If this cannot be achieved rest breaks must be planned.
The timing and length of breaks is not laid out in the regulations. It is recommended that breaks are shorter and more frequent, are taken before employees get tired and are taken away from the screen.
Eyesight tests
If users of DSE (or those about to become users) request an eye and eyesight test then employers have to pay for it. If such tests show they need special glasses specifically for DSE work, then again the employer would have to pay for a basic pair of frames and lenses.
Users are entitled to further tests at regular intervals after the first test, and in between if they are having problems. The regular intervals are usually prescribed by the optician carrying out the test.
Employers can decide how to provide eyesight tests. Such tests can be arranged by users and refunded by the employer, or the employer can chose an optician and send all users there. Factors to consider include:
- Contacting a number of opticians to get charges
- Ask whether the opticians will come to the Company
- Ask for standard information about the employees tested (when re tests are needed, whether glasses are needed)
- Advise users what procedures are in place
- Have a clear policy on what is paid for and what is not paid for, which is passed onto users.
Home/Remote Working
Policy
We recognise the importance of ensuring that all home and remote working activities are identified and managed appropriately to minimise the risks to both the employer and employee. The health, safety and welfare of home and remote workers will always be carefully considered with the aim to provide the same levels of protection as employees who work on-site so far as reasonably practicable. Home working and remote working offers many advantages to both the employer and employee, but it also brings its own health and safety hazards. Common hazards associated with home/remote workers include working in isolation, stress and mental well-being, lone working, use of computers/work equipment, fire, manual handling, travelling and a lack of control over the working environment. Due to the many activities and hazards which may arise from home/remote working, this policy should not be read and acted upon in isolation, but cross referenced to other relevant sections and guidance within the companies health and safety policy.
We will assess the potential work activities and hazards from home/remote working and take appropriate action to ensure adequate control measures are in place to reduce risk. We will take into account not only the task but also the abilities and experiences of those who may be undertaking the work. The findings of the risk assessments will determine the level of supervision required. To ensure that home/remote workers are not put at more risk than other employees we will provide adequate training and information on understanding the risks and controls measures required in order to reduce the risk associated with home/remote working and the tasks undertaken.
Checks will be made to ensure that any home/remote workers have no medical condition which makes them unsuitable for home or remote working. We will not permit home or remote working where risks cannot be controlled to an acceptable level. Procedures will be put in place to monitor home and remote workers to ensure they remain safe. We will regularly review and, where necessary, modify our assessments, especially where we have reason to suspect that they are no longer valid or there has been a significant change in the work to which the assessment relates.
Arrangements for Home/Remote Working
The Home/Remote Working Co-ordinator will ensure that:
1.1 All employees likely to work from home or remotely are identified.
1.2 Consultation with employees regarding home and remote working takes place and Home Working Checklist have been completed by the employee and signed by the line manager.
1.3 The tasks and work activities which will be undertaken by home/remote workers are identified and listed.
1.4 The hazards to which employees may be exposed during home/remote working are suitably and sufficiently assessed.
1.5 Adequate control measures are implemented to prevent ill health and accidents.
1.6 A decision based on the risk assessment findings is made to determine the level of supervision and frequency required.
1.7 Activities requiring special arrangements in order to monitor the safety of home/remote workers are identified.
1.8 Activities which must not be performed by home/remote workers are identified and brought to the attention of all relevant persons.
1.9 Employees that work from home or remotely are given adequate information, instruction and training in order to perform the task safely and effectively.
1.10 Checks are made to ensure that any home/remote workers are medically fit for the tasks where necessary.
1.11 Control measures and risk assessments are regularly monitored and maintained to ensure they remain effective.
Guidance and Records
Home and Remote Working Activities Introduction
Home and remote working is a way of working ‘at a distance’, using information technology (IT) to allow employees to undertake work away from the employers' premises. Home and remote workers can be based at home, occasionally work from home/remotely, or be mobile. This will often involve many different work activities and environments, which each bring their own health and safety hazards.
Due to the varied nature of the activities undertaken by home and remote workers, organisations will need to look at the risks from both perspectives, your organisations and the individual worker’s. The importance of effective consultation, co-operation, communication and undertaking risk assessments which are relevant to each individual home/remote worker is of paramount importance to the company.
The guidance contained in this policy should not be treated in isolation as it may be necessary to consult other relevant sections of the policy (particularly Lone Working), depending on the type of work and environment encountered by the home/remote worker. Therefore we strongly recommend that you consult your health and safety consultant or call SafeWorkforce on 01484 439930, option 3, in order clarify any particular matters which relate to home or remote working.
Listed below is generic guidance which relate to home and remote workers and includes information on good practice. However, it should be recognised that each home/remote worker will be different including the standards and guidance applied which are dependent on individual circumstances.
Communication and Consultation
Effective health and safety management relies on good communication between the company and home/remote workers given their isolated working arrangements. As homeworkers spend a limited time on-site, the issue of communication and providing information cannot be addressed in the same way as for employees who are on site for regular periods. In smaller firms a close working relationship between the company/managers and homeworkers may permit a more informal approach to communication.
Although informal communication between managers and home/remote workers may be effective in smaller companies more formalised approaches to communication are essential in larger organisations. The method and frequency of communication will vary but should be agreed between the company/manager and the home/remote worker.
Companies should provide home/remote workers with written details of their responsibilities and contact details, employee “Code of Conduct” handbooks and any necessary information they would need. This should include copies of risk assessments and work procedures, Display Screen Assessments and completed Homeworker’s Checklist which can be found in Appendix 1.
A lot of emphasis is put on supplying information to home/remote workers, but it is also important to supply information on managing home/remote workers to line management. Types of information that are useful include: competencies involved; how to manage high levels of trust and low levels of control; how to empower staff to work independently; information to help line managers support homeworkers and avoid potential consequences of lone working such as stress or isolation; and the setting of clear goals.
Any incidents affecting home/remote workers need to be communicated to and recorded by employers. This includes accidents and any ‘near miss’ occurrences. Employees need to know the procedures for reporting work-related accidents and ill health or any health and safety concerns. All reports received should be investigated by the line manager. Competent health and safety or occupational health support can be provided by your health and safety consultant or by contacting SafeWorkforce on 01484 439930, option 3.
It is important to make sure that home/remote workers do not feel divorced from decision-making about their work and workplaces. Consultation, involvement and representation of home/remote workers should also be encouraged because they are effective ways of determining whether health and safety arrangements are good enough, and of making improvements.
Risk Assessment
Risk assessments should be undertaken that are specific to each home/remote worker’s work environment and involve the home/remote worker in the process of identifying potential hazards. Companies should ensure that the risk assessments which have been carried out for individual home/remote workers have addressed a range of significant hazards in the home workplace (e.g. electrical; manual handling; chemicals; ventilation; lone working/isolation) and include potential hazards that would not normally be found in a workplace such as pets.
In assessing the risk of a task that a home/remote worker will undertake, it is important to consider the interaction of the task and the home environment, and not just accept the risk assessment developed for the process on the work site. There can be differences between the home and work site that mean the risk can be higher for the task when performed in the home environment.
Risk assessments carried out for home/remote workers should also identify who else may be at risk, such as family and vulnerable persons (e.g. children, and new or expectant mothers). Regular reviews of risk assessments should be carried out to ensure that there have been no significant changes.
Further detailed information on how to undertake risk assessments can be found in the policy section on risk assessments, although it may be necessary to undertake specialist risk assessments including COSHH assessments, display screen assessments and manual handling.
Putting in place clear, consistent management systems will reduce risks to home/remote workers, but it is only through regular monitoring that you can be sure risks are being controlled adequately and the systems are effective. Home/remote workers’ managers or an appointed assessor should make regular enquiries to make sure the employee is following safe practices and not experiencing aches or symptoms of stress. You should review risk assessments regularly and involve the employees affected. If it is not practical for managers to visit home/remote workers, the employees could complete a regular self-assessment of risk, which their line manager would check and discuss with them.
Work Environment
There is a fine line between taking reasonable precautions and invading personal privacy. However, companies will need to assess the risks of issues such as available space and lighting and the working environment.
As a minimum, there should be enough room for work to be carried out, including space for the workstation, other equipment (e.g. printers) and storage of materials. If the employee is working permanently from home, they should ideally choose one room as their office. This reduces physical intrusion into the home, helps keep domestic interruptions to a minimum and reduces risks to other people at home (e.g. young children). If the room is lockable, so much the better – this improves the security of your equipment and data. Sheds and garages are not generally recommended for home/remote working because it is often impossible to control security and the working environment.
You should also be careful about letting your staff choose attics and cellars, because these spaces often have limited access, poor temperature or ventilation control and a lack of natural light. General health and safety hazards need to be considered by both the employer and the worker because employers have little direct control over the home workplace.
There should be suitable access to the work room and the employee needs to ensure good standards of housekeeping, including adequate lighting, removing trailing leads and not using the floor or high shelves for storage. Home/remote workers must make sure they use equipment correctly and take reasonable care of their own health and safety. They must also be aware of the risks their work poses to other people, such as family members (including children).
If your staff are working at other employers’ workplaces as outsourced contract staff, the health and safety arrangements and responsibilities should be included in a contract. This agreement must ensure, as a minimum that a suitable workspace is provided and emergency arrangements are clear, and it must specify who is responsible for carrying out risk assessments and providing workstation equipment.
Work Equipment
You should apply similar furniture and equipment standards to a home workstation as you would in an office. A suitable desk and adjustable chair will normally be needed. These should be ergonomically designed to reduce the risk of musculoskeletal problems. Allowing employees some choice in style will enable them to choose equipment that suits the décor of their house. You may need to provide accessory equipment, such as task lighting to supplement domestic lighting. Some work or office equipment (e.g. certain types of shredder) is not suitable for domestic situations where young children are present. In these cases it may be more appropriate to supply equipment intended for domestic use. If employees only occasionally work from home, it is generally fine for them to use their own equipment to log in to work networks.
Permanent computer workstations need to be competently assessed and legally compliant as a minimum. Accessories such as footrests and document holders may be necessary – this will be determined by the workstation risk assessment. If the employee is travelling from place to place, their equipment needs to be light and portable. In such cases a laptop is typically provided. Laptops can themselves present a hazard, as they have limited adjustability. Minimising the amount of time spent using a laptop, and taking regular rest breaks, will help. If an employee is based at home and uses a laptop regularly for long periods at the same workstation, you will need to provide accessories, such as a mouse, keyboard, screen (or laptop riser) or docking station. The specific details should be determined through the workstation assessment, taking account of the user’s needs, space restrictions and how long they spend at the computer.
Maintaining equipment and electrical safety
Any work equipment including electrical equipment provided by the company and given to the home/remote worker will need to be maintained in good condition and will be the responsibility of the company. You will need to consider how you will carry out scheduled and breakdown maintenance of work equipment.
You can help reduce frustration and wasted work time by providing: good instruction and training on how to use software and manage minor equipment failures. Portable electrical items from laptops to mobile phone chargers require regular inspection to check that they are still safe. Some equipment may also need combined inspection and testing. IT equipment often requires only visual inspection by a competent person. This could be done by the employee (after suitable training) or during monitoring visits. Choosing low-voltage or double insulated equipment means the need for regular electrical testing can be minimised.
Companies cannot be responsible for the whole domestic electrical system at your employees’ homes. Nevertheless, if you have concerns about electrical safety or the availability of sockets (leading to trailing leads or over-use of extension leads), you will need to agree with the employee how these hazards will be controlled.
Mental Wellbeing
Remote working hazards extend beyond the physical work environment. Working arrangements are also important. For example, some employees may find it difficult to adapt to working in an environment with limited social contact, while others may find it harder to manage their time or to separate work from home life. For these reasons it is important to consider competence in areas such as time and self-management at the recruitment and selection stage, or before allowing existing employees to work from home.
Employees need to be aware of issues of time management and social isolation and they must realise that working from home is not always an easy option. Those who apply to work from home thinking that it will give them an opportunity to juggle their work around a busy home life may find that the opposite is true, as it can be difficult to turn off the computer and close the office door at the end of the day, especially when deadlines are looming. Home/remote workers may be tempted to work longer than normal hours, due to the lack of direct supervision.
Give your staff some practical training and tips on how to separate their work and home lives. Lone working is also a major consideration for employees working at home and while travelling. All remote workers (including those working at another employer’s premises) risk feeling isolated, and some people can find this stressful.
It is important to maintain good communication systems and formal means of contact with remote workers to minimise feelings of isolation. How you do this will depend on the number of remote workers you are dealing with and what they are doing, but you should consider: regular one-to-one meetings between remote workers and their line managers, either at the employee’s house or an agreed location. Regular meetings between home/remote workers and their co-workers, give employees the opportunity to network and get to know each other and help maintain effective teamwork.
Lone Working
Organisations will also need to consider and assess the risk that an employee might suffer an accident, illness or assault while they are working alone remotely or at home. In many cases there will not be much difference between the risk while travelling and the risk while working alone in other ways. However, sometimes employees may have to visit people or places where they feel more vulnerable or may be at greater risk. Companies should ensure that all of these team members have information on how to stay safe when working and travelling alone. It is good practice to have a system for checking the whereabouts of workers who travel alone. As a minimum, the employee should record full details of where they are going and their expected travel time. At the end of the working day, either the employee should ring or text an agreed contact or ‘buddy’ to say they are home or a family member should have details of who to contact if they have any concerns.
Further guidance and procedures are fully documented in the “Lone Worker” section of the companies’ health and safety policy and should be read in conjunction with this section of the policy and guidance.
Health and Safety Legislation Relevant to Home/Remote Working:
- The Health and Safety at Work, etc Act (HSWA) 1974
- The Management of Health and Safety at Work Regulations 1999
- The Control of Substances Hazardous to Health Regulations (COSHH) 2002
- The Manual Handling Operations Regulations 1999
- The Control of Noise at Work Regulations 2005
- The Health and Safety (Display Screen Equipment) Regulations 1992 (as amended in 2002)
- The Provision and Use of Work Equipment Regulations 1998
- The Personal Protective Equipment at Work Regulations 1992
- The Health and Safety (First Aid) Regulations 1981
- The Reporting of Injuries, Diseases and Dangerous Occurrences Regulations 2013 (RIDDOR)
- The Safety Representatives and Safety Committees Regulations 1977
- The Health and Safety (Consultation with Employees) regulations 1996
- The Electricity at Work Regulations 1989